Zirconia Ceramic
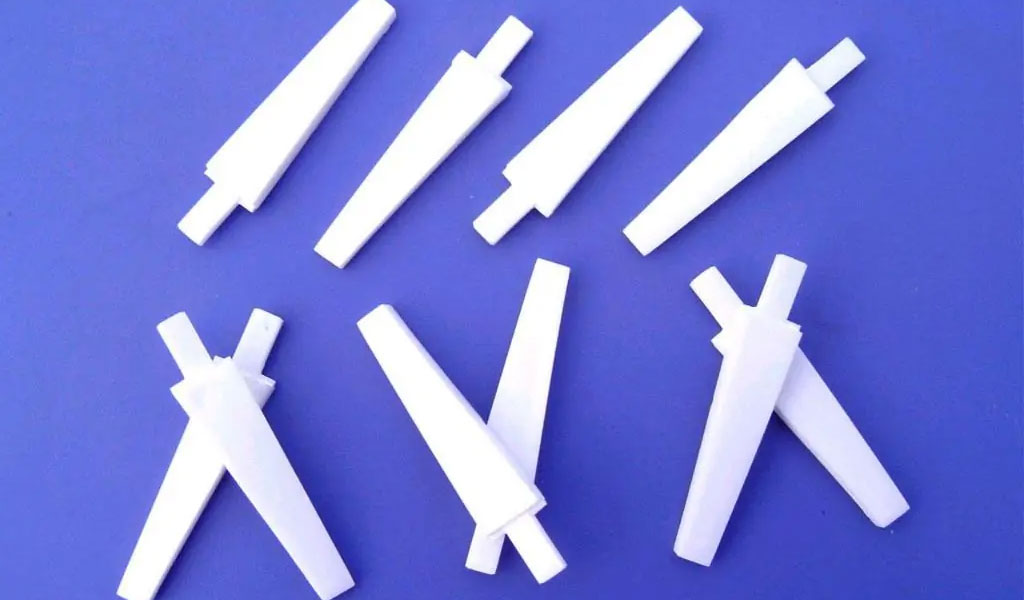
What Is Zirconia Ceramic
The reserves of zirconium in the earth’s crust exceed those of metals such as Cu, Zn, Sn, and Ni, and the resources are abundant. The world’s proven zirconium resources are about 19 million tons (calculated as metal zirconium), and there are about 20 kinds of ores, mainly containing the following compounds:
- Zirconium dioxide (monoclinic zirconium and its various variants); .
- Zirconium orthosilicate (zircon and its various variants);
- Compounds such as sodium zirconium silicate, calcium, iron (anisotropic stone, negative anisotropic stone, zirconium diamond).
The content of zirconium in anisotropy and negative anisotropy is very low and has no industrial value, so the main source of zirconium is monoclinic zircon and zircon, among which zircon is widely distributed. Pure ZrO2 is white and contains Impurities are yellow or gray, generally contain HfO2, and are not easy to separate.ZrO2 has excellent properties such as high melting point and boiling point, high hardness, insulator at room temperature, and electrical conductivity at high temperature.
Since the 1920s, it has been used as a refractory material for melting glass and smelting steel. Since the 1970s, with a deeper understanding of ZrO2, people have further researched and developed ZrO2. as structural and functional materials. In 1975, Australian R. G. Garvie made partially stabilized zirconia ceramics (Ca-PSZ) with CaO as stabilizer, and used the toughening effect of ZrO2 martensitic transformation for the first time to improve toughness and strength, which greatly expanded the structure of ZrO2. Applications in the field of ceramic concave.
Zirconia ceramic, ZrO2 ceramics, Zirconia Ceramic have excellent properties such as high melting point and boiling point, high hardness, insulator at room temperature, and electrical conductivity at high temperature. Zirconia ceramic is white, yellow or gray when it contains impurities, generally contains HfO2, and is not easy to separate.There are three crystalline states of pure ZrO2 under normal pressure. The production of zirconia ceramics requires the preparation of powders with high purity, good dispersion properties, ultra-fine particles and narrow particle size distribution.There are many preparation methods for zirconia ultra-fine powder.The purification of zirconia mainly includes chlorination and thermal decomposition, alkali metal Oxidative decomposition method, lime melting method, plasma arc method, precipitation method, colloid method, hydrolysis method, spray pyrolysis method, etc.
Zirconia Ceramic CNC Machining Services – Custom Zirconia Ceramic Machined Parts Manufacturer & Company
Zirconia Ceramic products are in demand due to their popularity in the electronic and medical industry, Pintejin is a China top Zirconia Ceramic CNC machining company that fabricates quality zirconia ceramic machined parts as your request. We can provide cost-effective solutions for industries ranging from medical, chemical, oil & gas, electronics, construction, and more. The fabrication process will have an impact on the performance of the zirconia ceramic parts. CNC manufacturing usually works with industry zirconia ceramic and is often used to make industrial components including gears, valves, bushes, manifolds, insulators, and fittings. Pintejin has years of experience in precision machining and always keeps up with the most advanced processing technique and equipment, our purpose is to employ the optimal tools and parameters during the CNC zirconia ceramic machining and get the best surface finishes and tolerances of zirconia ceramic machined parts effectively.
Zirconia Ceramic Machined Parts
The Pintejin promise is the delivery of the quantity you need, when you need it, without fail. This pledge is backed by a level of Ceramic-specific knowledge and experience the average machine shop simply doesn’t possess. We understand the unique characteristics of both high performance and standard utility zirconia ceramic. Pintejin engineers and machining professionals know the ideal spindle speeds and feed rates for ceramic machining success. They are aided by an in-house tooling department equipped to create the highly accurate tools a zirconia ceramic machining project demands.
The Type And Characteristics Of Zirconia Ceramic
Pure ZrO2 is white, yellow or gray when it contains impurities, and generally contains HfO2, which is not easy to separate. The world’s proven zirconium resources are about 19 million tons, and zirconia is usually obtained by purifying zirconium ore. There are three crystal states of pure ZrO2 at normal pressure: monoclinic zirconia (m-ZrO2), tetragonal zirconia (t-ZrO2) and cubic (Cubic) zirconia (c-ZrO2). Types exist in different temperature ranges and can be converted into each other:
- Monoclinic Zirconia (m-ZrO2)- Temperature: <950℃- Density: 5.65g/cc
- Square Zirconia (t-ZrO2)- Temperature: 1200-2370℃- Density: 6.10g/cc
- Cubic Zirconia (c-ZrO2)- Temperature:>2370℃- Density:6.27g/cc
The above three crystal states have different physical and chemical properties. In order to obtain the desired crystal shape and performance in practical applications, different types of stabilizers are usually added to make different types of zirconia ceramics, such as partially stabilized zirconia (partially stabilized zirconia, PSZ), when the stabilizer is CaO, MgO, Y2O3, it is expressed as Ca-PSZ, Mg-PSZ, Y-PSZ, etc. respectively. The tetragonal zirconia composed of metastable t-ZrO2 is called tetragonal zirconia polycrysta (TZP). When the added stabilizers are Y2O3 and CeO2, they are expressed as Y-TZP, Ce-TZP, etc. respectively.
The Powder Preparation Of Zirconia Ceramic
The production of zirconia ceramic requires the preparation of powders with high purity, good dispersion properties, ultra-fine particles and narrow particle size distribution. There are many preparation methods for zirconia ultra-fine powder. The purification of zirconia mainly includes chlorination and thermal decomposition, alkali metal Oxidative decomposition method, lime melting method, plasma arc method, precipitation method, colloid method, hydrolysis method, spray pyrolysis method, etc. Powder processing methods include co-precipitation method, sol-gel method, evaporation method, supercritical synthesis method, microemulsion method, hydrothermal synthesis method, network and vapor deposition method.
The Production Process Of Zirconia Ceramic
The Forming Of Zirconia Ceramic
The molding of zirconia ceramics includes dry pressing molding, isostatic pressing molding, grouting molding, hot die casting molding, tape casting, injection molding, plastic extrusion molding, colloidal solidification molding, etc. The most widely used are injection molding and dry pressing.
- Grouting:The molding process of grouting includes physical dehydration process and chemical coagulation process. Physical dehydration removes the water in the slurry through the capillary action of the porous gypsum mold. The chemical coagulation process is because Ca2+ generated by the dissolution of CaSO4 on the surface of the gypsum mold improves the slurry. The ionic strength in the material causes the flocculation of the slurry. Under the action of physical dehydration and chemical coagulation, the ceramic powder particles are deposited on the gypsum mold wall. Grouting is suitable for the preparation of large-scale ceramic parts with complex shapes, but the quality of the green body, including shape, density, strength, etc., is poor, the labor intensity of workers is high, and it is not suitable for automated operations.
- Hot Press Injection Molding:Hot pressure injection molding is to mix ceramic powder with binder (paraffin) at a relatively high temperature (60~100 ° C) to obtain a slurry for hot die casting, and the slurry is injected into the metal mold under the action of compressed air to keep the Press cooling, demoulding to obtain a wax blank, the wax blank is dewaxed under the protection of inert powder to obtain a green body, and the green body is sintered at high temperature to become porcelain. The green body of hot press injection molding has accurate size, uniform internal structure, less mold wear, high production efficiency, and is suitable for various raw materials. The temperature of the wax slurry and the mold needs to be strictly controlled, otherwise it will cause under injection or deformation, so it is not suitable for manufacturing large parts, and the two-step firing process is complicated and energy consumption is high.
- Tape Casting:Tape casting is to fully mix ceramic powder with a large amount of organic binders, plasticizers, dispersants, etc. to obtain a flowable viscous slurry, add the slurry to the hopper of the casting machine, and use a scraper to control the thickness. It flows out to the conveyor belt through the feeding nozzle, and the film blank is obtained after drying. This process is suitable for the preparation of film materials. In order to obtain better flexibility, a large amount of organic matter is added, and the process parameters are required to be strictly controlled, otherwise it will easily cause defects such as peeling, streaks, low film strength or difficult peeling. The organic matter used is toxic and will cause environmental pollution, and a non-toxic or less toxic system should be used as much as possible to reduce environmental pollution.
The Degreasing And Degumming Of Zirconia Ceramic
In addition to the molding technology based on dry pressing, the products formed by other processes must be degreasing and degummed before being sintered in the furnace, because other processes except dry pressing will add a certain proportion of zirconium powder to the zirconium powder during molding. Plasticizers, these plasticizers must be removed after the product is formed, otherwise it will have a serious impact on the quality of the sintered product. Plasticizers are mainly composed of paraffin and other polymer materials. These materials are required to exhibit good plasticity and fluidity at a certain temperature, and have certain toughness and strength at room temperature.
The Sintering Of Zirconia Ceramic
The sintering methods that can be used for zirconia ceramics are usually:
- Pressureless sintering
- Hot pressing sintering and reactive hot pressing sintering
- Hot isostatic pressing (HIP)
- Microwave sintering
- Ultra-high pressure sintering
- Spark plasma sintering (SPS)
- In-situ pressure forming sintering Wait. Pressureless sintering is often used.
The Application Of Zirconia Ceramic
In terms of structural ceramics, zirconia ceramics are widely used in the field of structural ceramics due to their high toughness, high flexural strength and high wear resistance, excellent thermal insulation properties, and thermal expansion coefficient close to steel. Mainly include: Y-TZP grinding balls, dispersing and grinding media, nozzles, ball valve seats, zirconia molds, miniature fan shafts, fiber optic pins, fiber optic sleeves, drawing dies and cutting tools, wear-resistant knives, clothing buttons, Cases and straps, bracelets and pendants, ball bearings, light bats for golf balls, and other room temperature wear-resistant parts.
In terms of functional ceramics, its excellent high temperature resistance is used as induction heating tubes, refractory materials, and heating elements. Zirconia ceramics have sensitive electrical performance parameters and are mainly used in oxygen sensors, solid oxide fuel cells (SOFC) and high temperature heating elements. ZrO2 has a high refractive index (N-21^22), adding certain coloring elements (V2O5, MoO3, Fe2O3, etc.) to the ultra-fine zirconia powder, it can be made into colorful translucent polycrystalline ZrO2 materials , shining like a natural gemstone with brilliant and colorful light, it can be made into a variety of decorations. In addition, zirconia is being widely used in thermal barrier coatings, catalyst carriers, medical care, health care, refractories, textiles and other fields.
The Toughening Method Of Zirconia Ceramic
Zirconia is a special material. The toughening method is mainly achieved by using the phase transformation of zirconia!
Pure zirconia is a white solid, and when it contains impurities, it will appear gray or light yellow, and it can also display various other colors when a color developer is added. The molecular weight of pure zirconia is 123.22, the theoretical density is 5.89g/cm3, and the melting point is 2715℃. Usually contains a small amount of hafnium oxide, which is difficult to separate, but has no significant effect on the properties of zirconium oxide. Zirconia has three crystal forms: monoclinic, tetragonal, and cubic. At room temperature, zirconia only appears as a monoclinic phase, and when heated to about 1100 °C, it transforms into a tetragonal phase, and when heated to a higher temperature, it transforms into a cubic phase. Since a large volume change occurs when the monoclinic phase changes to the tetragonal phase, and a large volume change occurs in the opposite direction when cooling, it is easy to cause cracking of the product, which limits the application of pure zirconia in high temperature fields. . However, after adding the stabilizer, the tetragonal phase can be stabilized at room temperature, so there will be no sudden change in volume after heating, which greatly expands the application range of zirconia. The raw material used as stabilizer on the market is mainly yttrium oxide.