Ceramic Bearings
The performance comparison of four bearing materials of ordinary bearing steel AISI52100 (GCr15), stainless steel AISI440 (9Cr18), silicon nitride (Si3N4) and zirconia (ZrO2), ceramic bearing as an important mechanical foundation, because of its metal bearing Unparalleled excellent performance, high temperature resistance, super strength, etc. are leading the world of new materials. In the past ten years, it has been widely used in various fields of national economy and people’s livelihood.
Ceramic bearings have the characteristics of high temperature resistance, cold resistance, wear resistance, corrosion resistance, anti-magnetic and electrical insulation, oil-free self-lubrication, and high speed. It can be used in extremely harsh environments and special working conditions, and can be widely used in aviation, aerospace, marine, petroleum, chemical, automotive, electronic equipment, metallurgy, electric power, textiles, pumps, medical equipment, scientific research and defense and military fields. High-tech products for new material applications.
Custom Ceramic Bearings & Manufacturing – Online Ceramic Ball Bearings Supply
Precision Ceramic Machining services are ideal for manufacturing custom Ceramic Bearings needed for customers across a wide variety of industries and specialty applications. Pintejin is a ceramic parts online supplier providing top-quality Bearings and DIY ball Bearings made of other materials.Ceramic Bearings machining service at Pintejin can work with Zirconia Ceramic, Silicon Nitride Ceramic, Full Ball, Mixing Ceramic, etc. Our global custom machining network is optimized for production in flexible quantities. In addition to conventional turning, milling, and drilling processes, we also offer a ton of other fabrication services to take your unique design to realization with the help of professional engineers and seasoned workers. Our team can provide different custom metal finishing services for your Ceramic Bearings, such as anodizing and electro galvanizing.The comprehensive custom bearings production services make us a one-stop shop that provides the best quality control and competitive price.
The Case Studies Custom Ceramic Bearings
State-of-the-art equipment. Productions using versatile CNC machining centers and inspections using CMM and more accurate tools.Pintejin is your right ceramic parts machine shop with online quotes and fast shipping.
The Application Of Ceramic Bearings
Medical equipment, cryogenic engineering, optical instruments, high-speed machine tools, high-speed motors, printing machinery, food manufacturing machinery.
In the fields of aerospace, navigation, nuclear industry, petroleum, chemical industry, light textile industry, machinery, metallurgy, electric power, food, locomotive, subway, high-speed machine tools and scientific research, defense and military technology, etc. Working under special working conditions such as explosive, strong corrosion, vacuum, electrical insulation, non-magnetic, dry friction, etc., the indispensable substitute role of ceramic bearings is gradually being recognized by people.
With the continuous progress of machining technology and the increasing level of craftsmanship, the cost of ceramic bearings has continued to decline. It has been applied in a small range of high, precise and cutting-edge fields from the past, and has been gradually extended to various industrial fields of the national economy. Product market price It is also gradually approaching practicality and reaching a level acceptable to users. The wave of large-scale application of ceramic bearings has come!
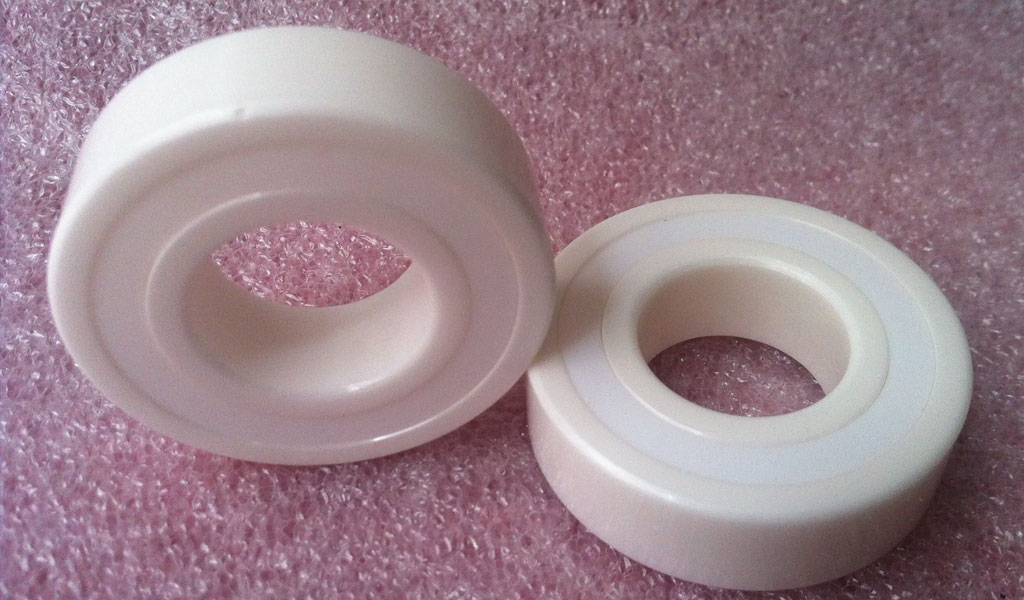
The Machining Category Of Ceramic Bearings
- High-speed bearing: It has the advantages of cold resistance, small force elasticity, high pressure resistance, poor thermal conductivity, light weight, and small friction coefficient. in high-precision equipment;
- High temperature bearing: The material itself has a high temperature resistance of 1200 °C, and is self-lubricating, and the operating temperature is between 100 °C and 800 °C without expansion due to temperature difference. It can be used in furnaces, plastics, steel and other high temperature equipment;
- Corrosion-resistant bearings: The material itself has the characteristics of corrosion resistance and can be used in strong acid, strong alkali, inorganic, organic salt, seawater and other fields, such as: electroplating equipment, electronic equipment, chemical machinery, shipbuilding, medical equipment, etc. .
- Antimagnetic bearing: Because it is non-magnetic, it does not absorb dust, which can reduce the peeling of the bearing surface, thereby reducing the running noise. Can be used in demagnetization equipment. Precision instruments and other fields.
- Electrically insulated bearing: due to high resistivity, it can avoid arc damage to the bearing, and can be used in various electrical equipment requiring insulation.
- Vacuum bearings: Due to the unique oil-free self-lubricating properties of ceramic materials, in the ultra-high vacuum environment, the problem that ordinary bearings cannot be lubricated can be overcome. Note: For the above five types of bearings, the same set of bearings can be used in high temperature, high speed, acid-base, magnetic field, non-insulation, but due to different material properties (please refer to the rare earth ceramic material performance table), when customers choose products, Choose the most suitable ceramic bearing material according to your application.
The Material Category Of Ceramic Bearings
The rings and rolling elements of ceramic bearings are made of all-ceramic materials, including zirconium oxide (ZrO2), silicon nitride (Si3N4), and silicon carbide (Sic). The retainer is made of polytetrafluoroethylene, nylon 66, polyetherimide, zirconia, silicon nitride, stainless steel or special aviation aluminum, thereby expanding the application surface of ceramic bearings.
Zirconia Ceramic Bearings
All-ceramic bearings have the characteristics of anti-magnetic and electrical insulation, wear resistance and corrosion resistance, oil-free self-lubrication, high temperature resistance and high cold resistance, and can be used in extremely harsh environments and special working conditions.
The ferrule and rolling element are made of zirconia (ZrO2) ceramic material, the cage is made of polytetrafluoroethylene (PTFE) as a standard configuration, glass fiber reinforced nylon 66 (RPA66-25), special engineering plastics (PEEK, PI), stainless steel (AISISUS316), brass (Cu), etc.
Silicon Nitride Ceramic Bearings
Silicon nitride full ceramic bearing rings and rolling elements are made of silicon nitride (Si3N4) ceramic materials.Generally, RPA66-25, PEEK, PI, and phenolic cloth bakelite tubes can also be used.
Compared with ZrO2 materials, all-ceramic bearings made of SiN4 can be used for higher speed and load capacity, as well as for higher ambient temperature.
At the same time, it can provide precision ceramic bearings for high-speed, high-precision and high-rigidity spindles, and the highest manufacturing accuracy is P4 to UP.
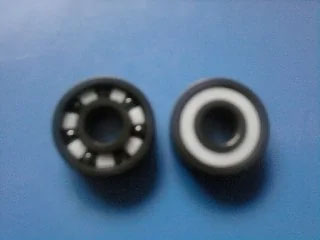
Ceramic Ball Bearings With Full Ball
The full-complement ball type full-ceramic bearing has a ball-filling notch on one side. Due to the design of the cage-free structure, more ceramic balls can be loaded than the standard structure bearing, thereby improving its load capacity and avoiding the limitation of cage materials. , can achieve the effect of corrosion resistance and temperature resistance of ceramic cage type all-ceramic bearings.
This series of bearings is not suitable for high rotation speed, and the notched surface should be installed at the end that does not bear the axial load during installation.
Mixing Ceramic Bearings
Ceramic balls, especially silicon nitride balls, have the characteristics of low density, high hardness, low friction coefficient, wear resistance, self-lubrication and good rigidity, and are especially suitable for rolling elements (inner and outer rings) of hybrid ceramic ball bearings with high speed, high precision and long life for metal).
Generally, the inner and outer rings are made of bearing steel (GCr15) or stainless steel (AISI440C), and the ceramic balls can be selected from ZrO2, Si3N4, or SiC materials.
The Advantage Of Ceramic Bearings
Ceramics are also more difficult to achieve a high-quality surface finish. It can grind them to a radium 0.1 surface finish, which allows a P5 accuracy class to be achieved. But ceramic bearings have the following advantages:
- First, because ceramics are almost not afraid of corrosion, ceramic rolling bearings are suitable for operation in harsh conditions full of corrosive media.
- Second, because the density of the ceramic rolling ball is lower than that of steel and the weight is much lighter, the centrifugal effect of the outer ring during rotation can be reduced by 40%, thereby greatly extending the service life.
- Third, ceramics are less affected by thermal expansion and contraction than steel, so when the bearing clearance is constant, the bearing can be allowed to work in an environment where the temperature difference changes more drastically.
- Fourth, because the elastic modulus of ceramics is higher than that of steel, it is not easy to deform when subjected to force, so it is beneficial to improve the working speed and achieve higher precision.
Ceramic bearing atomic structure, non-metallic intrinsic covalent bonds. This means that they share electrons, and this atom has a strong adsorption force, and for this reason, ceramic bearings offer some better performance than metal bearings. They are usually very stiff, elastic, and lightweight. This means that when the shape is changed, the load is applied in conjunction with improved wear properties.
Ceramic bearings run without lubrication. This is because the ceramic material is not microwelded. Micro-welding occurs when a flaw on the rolling element and raceway surfaces, usually with metals, interacts with another causing an arc. This reduces the surface and greatly reduces bearing life. Ceramic materials do not have this problem, which makes them suitable for a variety of applications that require a lube free environment. They usually behave in a stable manner at high temperatures which means there is less thermal expansion. It requires a lot more energy to increase the bond length of a covalent bond compared to a metal ionic bond.
Ceramics are non-metallic, non-ferrous materials. They do not corrode in the same way as metals when exposed to water and other harmful chemicals. Their high corrosion resistance allows their excellent performance in wet and chemically aggressive environments. Many engineering ceramics also have low densities, resulting in the bearing’s operating speed, which is improved due to low centripetal force and reduced friction. Due to the lack of free electrons in most ceramics, they are non-magnetic and excellent insulators. When researching ceramic bearings, the first thing one might notice is that they are basically more expensive than metal. There are many reasons.
There are extremely high energy and machining costs associated with the large amount of energy required to achieve the temperatures required for the high-grade feedstock sintering process. Because ceramics are so hard, machining and grinding costs increase rapidly when manufacturing precision bearings. All of this must be done in a clean environment with skilled labor. Ceramics are incredibly sensitive to impurities in their pores, so any contaminants may cause premature failure. As the size increases, the price also increases exponentially because of the high cost and the requirement of the machining method. These include the need for a slower sintering process in order to overcome temperature gradients in the green body, uniformly applying the amount of pressure in larger volumes and resulting machine cost.
Ceramic bearings have lower load carrying capacity compared to metals and are sensitive to thermal shock. Thermal shock is when a temperature gradient within a material causes differential expansion, which results in internal stress. This pressure can exceed the strength of such a material to form cracks.