Silicon Nitride Ceramic
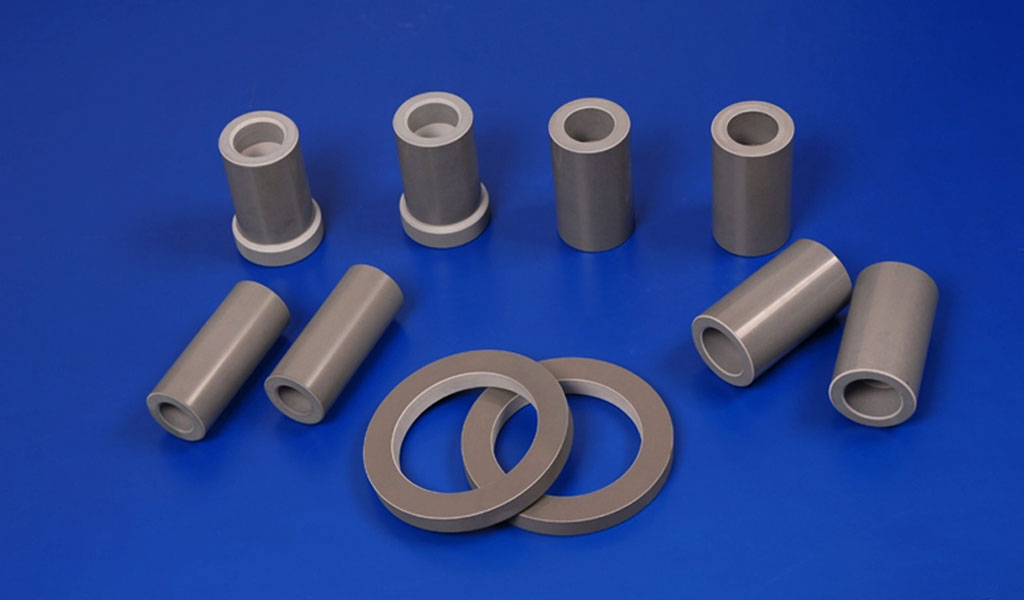
What Is Silicon Nitride Ceramic
Silicon Nitride is an inorganic substance with the chemical formula Si3N4. It is an important structural ceramic material with high hardness, lubricity, wear resistance, atomic crystal, and oxidation resistance at high temperature. Moreover, it can also resist the shock of cold and heat. It can be heated to more than 1000 ℃ in the air, and it will not be broken when it is rapidly cooled and then heated again. It is precisely because of the excellent properties of silicon nitride ceramics that people often use it to manufacture mechanical components such as bearings, gas turbine blades, mechanical seal rings, and permanent molds. If the heat-receiving surface of engine components is made of silicon nitride ceramics that are resistant to high temperature and difficult to transfer heat, it can not only improve the quality of diesel engines, save fuel, but also improve thermal efficiency. Such diesel engines have been developed in China, the United States, Japan and other countries.
Silicon nitride ceramic is an inorganic material ceramic that does not shrink during sintering. Silicon nitride is very strong, especially hot-pressed silicon nitride, which is one of the hardest substances in the world. It has the properties of high strength, low density and high temperature resistance.
Silicon Nitride Ceramic CNC Machining Services – Custom Silicon Nitride Ceramic Machined Parts Manufacturer in China
Silicon Nitride Ceramic variants can be machined using ceramic CNC machining services at Pintejin, which is a reliable supplier of precision machined parts, we can work well with a wide selection of thermoplastics. Based on years of experience and knowledge accumulation, we can produce most custom silicon nitride ceramic parts according to customer requirements and orders. CNC silicon nitride ceramic machining is a versatile and efficient manufacturing solution to get a large number of high-quality parts with complex geometries and high consistency. From design to silicon nitride ceramic material to production, we are well-equipped and skilled to help you gain the best outcome.
Silicon Nitride Ceramic Machined Parts
Silicon Nitride Ceramic machining parts have several key advantages compared to machining other materials. Silicon Nitride Ceramic turned parts and components are durable, cost-efficient, and even create a tighter seal for fittings. In addition, Silicon Nitride Ceramic machining and turning parts have a high heat and corrosion resistance! More importantly, Pintejin’s Silicon Nitride Ceramic machine parts are easy to machine and join, and made to your specifications and standards!
The Properties Of Silicon Nitride Ceramic Materials
As an excellent high-temperature engineering material, Si3N4 ceramic material can play the most advantage in its application in the high-temperature field. The future development direction of Si3N4 is:
- Make full use of the excellent characteristics of Si3N4 itself;
- In the sintering of Si3N4 powder, develop some new fluxes, research and control the best composition of the existing fluxes;
- Improve milling, molding and sintering processes;
- To develop the composite of Si3N4 and SiC and other materials in order to produce more high-performance composite materials.
The application of Si3N4 ceramics in automobile engines has created a new situation for the development of new high-temperature structural materials. The automobile industry itself is a multi-disciplinary industry that combines the culmination of various technologies. China is an ancient civilization with a long history and has made brilliant achievements in the history of ceramic development. With the process of reform and opening up, one day, China will also It is bound to rank among the major countries in the world’s auto industry and create greater glories for the development of the ceramic industry.
Many of the properties of silicon nitride are due to this structure. Pure Si3N4 is 3119, has two crystal structures, α and β, both of which are hexagonal. Its decomposition temperature is 1800 °C in air and 1850 °C in 110MPa nitrogen. Si3N4 has low thermal expansion coefficient and high thermal conductivity, so it has excellent thermal shock resistance. The hot-pressed sintered silicon nitride will not break even when it is heated to 1000℃ and put into cold water. At not too high temperature, Si3N4 has high strength and impact resistance, but it will be damaged with the increase of use time above 1200℃, reducing its strength, and it is more prone to fatigue damage above 1450℃, so Si3N4 The operating temperature generally does not exceed 1300 ℃. Since Si3N4 has a low theoretical density and is much lighter than steel and engineering superalloy steel, it is more appropriate to use Si3N4 ceramics to replace alloy steel in those places where materials are required to have high strength, low density, high temperature resistance, etc. .
It is extremely resistant to high temperature, and its strength can be maintained at a high temperature of 1200°C without decreasing. It will not melt into a melt after being heated, and will not decompose until 1900°C. And caustic soda solution below 30%, it can also resist the corrosion of many organic acids; at the same time, it is a high-performance electrical insulating material.
The Process Method Of Silicon Nitride Ceramic Materials
It is made of silicon powder as raw material, which is first formed into the desired shape by the usual molding method, and preliminary nitridation is carried out in nitrogen at a high temperature of 1200 ° C, so that a part of the silicon powder reacts with nitrogen to form silicon nitride. The whole body already has a certain strength. Then the second nitridation is carried out in a high temperature furnace of 1350℃~1450℃ to react into silicon nitride. Silicon nitride with a theoretical density of 99% can be obtained by hot pressing sintering.
The Preparation Of Silicon Nitride Ceramic Materials
The preparation technology of Si3N4 ceramics has developed rapidly in the past few years, and the preparation processes are mainly concentrated in the reaction sintering method, hot pressing sintering method, atmospheric pressure sintering method, and gas pressure sintering method. Due to different preparation processes, various types of silicon nitride ceramics have Different microstructures (such as porosity and pore morphology, grain morphology, intergranular morphology, and intergranular second phase content, etc.). Therefore, the performance varies greatly. In order to obtain Si3N4 ceramic materials with excellent performance, high-quality Si3N4 powder should be prepared first. The quality of Si3N4 powder prepared by different methods is not exactly the same, which leads to differences in its use. The failure of many ceramic material applications is often attributed to Because developers do not understand the differences between various ceramic powders, they have insufficient understanding of their properties. Generally speaking, high-quality Si3N4 powder should have the characteristics of high α-phase content, uniform composition, few impurities and uniform distribution in ceramics, small particle size and narrow particle size distribution and good dispersibility. The α phase in a good Si3N4 powder should account for at least 90%, because during the sintering process of Si3N4, part of the α phase will transform into the β phase, and there is not enough α phase content, which will reduce the strength of the ceramic material.
Reaction Sintering (RS)
The general molding method is adopted. First, the silicon powder is pressed into a green body of the desired shape, and then placed in a nitriding furnace for pre-nitriding (partial nitriding) sintering treatment. The pre-nitriding green body has a certain strength and can be Carry out various mechanical processing (such as turning, planing, milling, drilling). Finally, at the temperature above the melting point of silicon; the green body is again fully nitrided and sintered to obtain a product with little dimensional change (ie, after green body sintering, The shrinkage rate is very small, the linear shrinkage rate is < 011%). The product can be used without grinding. The reaction sintering method is suitable for the manufacture of parts with complex shapes and precise dimensions, and the cost is also low, but the nitriding time is very long.
Hot Press Sintering (HPS)
It is to heat-press and sinter Si3N4 powder and a small amount of additives (such as MgO, Al2O3, MgF2, Fe2O3, etc.) at a pressure above 1916 MPa and a temperature above 1600 °C. The hot-pressed sintered Si3N4 ceramics used by some companies in the United Kingdom and the United States have a strength as high as 981MPa or more. Additives and phase composition during sintering have a great influence on product properties. Due to the strict control of the composition of the grain boundary phase and proper heat treatment after the sintering of Si3N4 ceramics, it is possible to obtain Si3N4 series ceramic materials that do not significantly decrease in strength (up to 490MPa or more) even when the temperature is as high as 1300 °C, and the creep resistance Denaturation can be improved by three orders of magnitude. If the Si3N4 ceramic material is pre-oxidized at a high temperature of 1400-1500 ℃, the Si2N2O phase will be formed on the surface of the ceramic material, which can significantly improve the oxidation resistance and high temperature strength of the Si3N4 ceramic. The mechanical properties of Si3N4 ceramics produced by hot pressing sintering are superior to those of reaction sintering Si3N4, with high strength and high density. However, the manufacturing cost is high and the sintering equipment is complex. Due to the large shrinkage of the sintered body, the dimensional accuracy of the product is limited to a certain extent. It is difficult to manufacture complex parts. Only parts with simple shapes can be manufactured, and the machining of the workpiece is also difficult.
Atmospheric Pressure Sintering (PLS)
In terms of increasing the pressure of sintering nitrogen atmosphere, using the property of Si3N4 decomposition temperature rising (usually at N2 = 1atm pressure, it starts to decompose from 1800 ℃), after normal pressure sintering in the temperature range of 1700-1800 ℃, and then in Air pressure sintering is carried out in the temperature range of 1800-2000 ℃. The purpose of this method is to use air pressure to promote the densification of Si3N4 ceramics, thereby improving the strength of the ceramics. The properties of the obtained products are slightly lower than those of hot pressing sintering. The disadvantages of this method are similar to hot pressing sintering.
Gas Pressure Sintering(GPS)
In recent years, people have carried out a lot of research on air pressure sintering and achieved great progress. Gas pressure sintering of silicon nitride is carried out at a temperature of about 2000°C under a gas pressure of 1 to 10MPa. High nitrogen pressure suppresses pyrolysis of silicon nitride. Due to the use of high temperature sintering, the addition of less sintering aids is enough to promote the growth of Si3N4 grains, and obtain high-toughness ceramics with in-situ growth of long columnar grains with a density > 99%. Therefore, air pressure sintering can be used in laboratory It has received more and more attention in production. Gas pressure sintered silicon nitride ceramics have high toughness, high strength and good wear resistance, and can directly produce various complex shapes close to the final shape, which can greatly Reduce production cost and processing cost. And its production process is close to cemented carbide production process, suitable for mass production.
The Research Status Of Silicon Nitride Ceramic Materials
For Si3N4 and Sialon ceramic sintered bodies, a process for forming by superplasticity without forming a composite material and maintaining a single state has been provided, and a sintered body formed according to the process is provided. Silicon nitride and Sialon sintered body with a relative density of more than 95% and a linear density of 50 μm in the two-dimensional cross section of the sintered body in the range of 120 to 250; Compression causes plastic deformation to take place at strain rates of less than 10-1/sec. The formed sintered body has excellent mechanical properties especially at normal temperature.
Si3N4 ceramic is an important structural material. It is a superhard material, which has lubricity and wear resistance. Except for hydrofluoric acid, it does not react with other inorganic acids, and has strong corrosion resistance and high temperature resistance. Oxidation. And it can resist the shock of cold and heat. It can be heated to more than 1,000 ℃ in the air, and it will not be broken after rapid cooling and rapid heating. It is precisely because of the excellent properties of Si3N4 ceramics that people often use it to make bearings. , gas turbine blades, mechanical seal rings, permanent molds and other mechanical components. If the heating surface of engine components is made of silicon nitride ceramics that are resistant to high temperature and difficult to transfer heat, it can not only improve the quality of diesel engines, save fuel, but also improve thermal efficiency. . China, the United States, Japan and other countries have developed this diesel engine.
The Related Applications Of Silicon Nitride Ceramic Materials
Taking advantage of the light weight and stiffness of Si3N4, it can be used to manufacture ball bearings, which have higher precision than metal bearings, generate less heat, and can operate at higher temperatures and corrosive media. The steam nozzles made of Si3N4 ceramics have the characteristics of wear resistance and heat resistance. They have no obvious damage after being used in a 650°C boiler for several months, while other heat and corrosion resistant alloy steel nozzles can only be used for 1-2 months under the same conditions. .Si3N4 glow plug jointly developed by Shanghai Institute of Silicate, Chinese Academy of Sciences and Shanghai Institute of Internal Combustion Engine, Ministry of Mechanical and Electrical, solves the problem of difficult cold start of diesel engines, and is suitable for direct injection or non-direct injection diesel engines. This glow plug is the most advanced and ideal diesel engine ignition device available today. The Japan Institute of Atomic Energy and Mitsubishi Heavy Industries successfully developed a new crude pump with a rotor composed of 11 Si3N4 ceramic turntables in the pump casing. Because the pump adopts Si3N4 ceramic rotor with small thermal expansion coefficient and precise air bearing, it can operate normally without lubrication and cooling medium. If this pump is combined with an ultra-vacuum pump such as a turbo-molecular pump, a vacuum system suitable for nuclear fusion reactors or semiconductor processing equipment can be formed.
The above are just a few application examples of Si3N4 ceramics as structural materials. It is believed that with the improvement of Si3N4 powder production, molding, sintering and processing technology, its performance and reliability will continue to improve, and silicon nitride ceramics will be more widely used. Due to the improvement of the purity of Si3N4 raw materials, the rapid development of Si3N4 powder molding technology and sintering technology, and the continuous expansion of application fields, Si3N4 is taking an increasingly important position in the industry as an engineering structural ceramic. Si3N4 ceramics has excellent comprehensive properties and abundant resources, and is an ideal high-temperature structural material with broad application fields and markets, and all countries in the world are competing for research and development. Ceramic materials have the characteristics of wear resistance, corrosion resistance, high temperature resistance, oxidation resistance, thermal shock resistance and low specific gravity that are difficult to compare with general metal materials. It can withstand the harsh working environment that metal or polymer materials are incapable of, and has a wide range of application prospects. After metal materials and polymer materials, it has become the key basic material supporting the pillar industry in the 21st century, and has become one of the most active research fields. Today, countries around the world attach great importance to its research and development. As one of the important members of the high-temperature structural ceramics family The first Si3N4 ceramics have more excellent mechanical properties, thermal properties and chemical stability than other high-temperature structural ceramics such as oxide ceramics and carbide ceramics. Therefore, they are considered to be the most promising materials in high-temperature structural ceramics.
It can be predicted that with the continuous progress of basic research and new technology development of ceramics, especially the improvement of the preparation technology of complex parts and large parts, Si3N4 ceramic materials will be more widely used as engineering materials with excellent performance.
Silicon nitride is very strong, especially hot-pressed silicon nitride, which is one of the hardest substances in the world. It is extremely resistant to high temperature, and its strength can be maintained at a high temperature of 1200°C without decreasing. It will not melt into a melt after being heated, and will not decompose until 1900°C. And caustic soda solution below 30%, it can also resist the corrosion of many organic acids; at the same time, it is a high-performance electrical insulating material.
Silicon Nitride – Properties Chemical formula Si3N4. White powdery crystal; melting point 1900 ℃, density 3.44 g/cm (20 ℃); there are two variants: α type is a hexagonal close-packed structure; β type is a spar-like structure. Silicon nitride is gray when it has impurities or excess silicon.
Silicon nitride hardly interacts with water; it is slowly hydrolyzed in concentrated strong acid solution to generate ammonium salt and silicon dioxide; it is easily soluble in hydrofluoric acid and does not work with dilute acid. Concentrated strong alkali solution can slowly corrode silicon nitride, and molten strong alkali can quickly convert silicon nitride into silicate and ammonia. Silicon nitride can reduce transition metal (see transition element) oxides, lead oxide, zinc oxide and tin dioxide at temperatures above 600 °C, and release nitrogen oxides and nitrogen dioxide. At 1285°C, silicon nitride reacts with tricalcium nitride Ca3N2 as follows:
Ca3N2+Si3N4─→3CaSiN2
The preparation methods of silicon nitride are as follows: at 1300~1400℃, the powdery silicon is reacted with nitrogen; at 1500℃, the pure silicon is reacted with ammonia;
The mixture of silica and carbon is fired in nitrogen containing a small amount of hydrogen; Si(NH2)4, the ammonolysis product of SiCl4, is completely thermally decomposed. Silicon nitride can be used as catalyst carrier, high temperature resistant material, coating and abrasive, etc.
Silicon nitride ceramics have the characteristics of high strength and high temperature resistance. Among the ceramic materials, it has the best comprehensive mechanical properties, thermal shock resistance, oxidation resistance, wear resistance and corrosion resistance. It is the first ceramics for heat engine components. a candidate material. In the machinery industry, silicon nitride ceramics are used as bearing balls, rollers, ball races, tools and dies, new ceramic tools, pump plungers, and mandrel sealing materials.
In the chemical industry, silicon nitride ceramics are used as wear and corrosion resistant parts. Such as ball valves, pump bodies, combustion vaporizers, filters, etc.
In the metallurgical industry, silicon nitride ceramics have self-lubricating properties due to their high temperature resistance and small friction coefficient. It is stable to most metals and alloy solutions. Therefore, it can be used to make tools and dies for metal material processing, such as pulling mandrels, extrusion, wire pulling dies, rolls, transfer rolls, heating element fixtures, thermocouple sets, and metal heat treatment supports. , Crucible, aluminum liquid guide camp, aluminum lining, etc.
Silicon nitride ceramic materials are also widely used in electronics, military and nuclear industries.
Physical and chemical properties of silicon nitride ceramic powder and technical indicators of products
- Silicon nitride ceramic is a white-gray powder with the molecular formula: SI3N4;
- Molecular weight: 140.3 , density 3.2g/cm³
- Its chemical composition: N>38-39; 0<1-1.5; C<0.1; Fe<0.2.
- Granularity depends on user requirements.