Powder Metallurgy Dies
Pintejin Ceramic Machining Shop uses powder metallurgy dies technology to replace traditional silicone molds and machining processes to produce ceramic parts, which has the advantages of high material utilization, uniform structure, high precision parts manufacturing, light weight, wear resistance, etc. And same time,reduce production costs and improve production efficiency.
What Is Powder Metallurgy Dies
The mold technology of powder metallurgy is the key technology for the production and development of powder metallurgy mechanical parts. The level of mold life not only affects product quality, but also affects production efficiency and production cost.
With the rapid development of machinery, electronics, national defense and other industries, the superiority of powder metallurgy mold forming technology in the production of high-quality, high-yield and low-consumption mechanical parts is prominent. Especially in the current situation of the rapid development of the electronics and automobile industries, the development of industrial products has higher and higher requirements for molds.
The powder metallurgy mold has requirements on the charging ratio and the uniformity of the structure and density of the pressed blank, so in addition to the cavity design of the mold, in the design of the overall mold and the mold base, mechanical design or The relevant structures in the mold design, they are combined with the press and mold forming parts and connecting parts to meet the forming requirements of the powder metallurgy mold.
Since there are many powder pressing methods, powder pressing dies are also varied. According to different pressing methods, it can be divided into: pressing dies, finishing dies, compound pressing dies, forging dies and so on.
The basic principles of powder metallurgy mold design are:
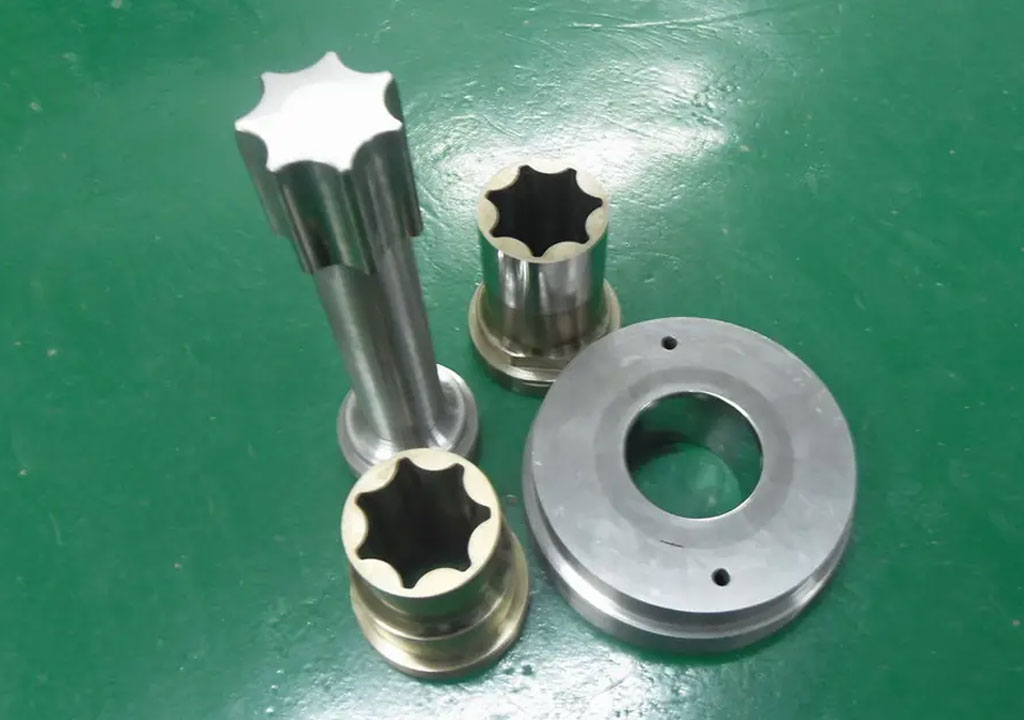
- Give full play to the process characteristics of less powder metallurgy, no cutting processing and near-form forming to ensure that the blank meets the three basic requirements of geometry and size, precision and surface roughness, density and distribution, whether it is a pressing die, a finishing die, etc. , recompression die, forging die are required.
- Among them, especially the density and distribution of pressed blanks and forged blanks are the main technical indicators in die design;
- Reasonable design of mold structure and selection of mold materials, so that mold parts have high enough strength, rigidity and hardness, high wear resistance and service life, to meet the requirements of high-pressure working container safe, reliable and easy to operate;
At the same time, pay attention to the machinability and interchangeability of the mold structure and mold parts, and reduce the cost of mold manufacturing. The design steps and basic methods are as follows:
- First of all, understand and master the relevant design data, as an important basis for mold design;
- Secondly, carry out material design and process design according to product requirements, carry out green compact design or preform design according to product drawings, select press and pressing method, and design mold structure sketch;
- Then take the blank size as the basic basis, consider the size changes in the process, calculate the size of the main mold parts separately, generally first calculate the size directly related to the mold cavity, and then calculate the size of other mold parts according to the mold assembly relationship;
- Finally, draw the mold assembly drawing and part drawing, according to the different working requirements of various molds, mark the dimensional deviation and geometric tolerance, and select the mold material and technical requirements.
Powder Metallurgy Dies & Tooling & Mold Making Service Online
Pintejin ceramic machining shop is one of the best Powder Metallurgy mold makers in China, offering ceramic molding solutions for every industry, including medical powder metallurgy dies, electrical powder metallurgy dies, automotive powder metallurgy dies and more. In order to meet our clients’ large demand for ceramic parts, we cooperate with reliable partners to offer powder metallurgy dies making services, which can make up for your one-stop requirements for ceramic prototype and mass production. Our main services offering include mold design, mold making & ceramic parts production, as well as with CNC machining. With more than 10 years of experience, we are able to produce custom affordable zirconia, alumina, silicon ni- tride, silicon carbide, aluminum nitride, microporous ceramics according to customers’ specifications, drawings or samples. We own advanced techniques, highly skilled staff that employ superior tooling and molding processes to ensure that the mold parts are of the cheapest price and highest quality. Whether you need rapid tooling, mass production mold making with tight tolerances, our team of experienced specialists can offer a cost-effective solution at each stage. Contact our expert team and get a price for your tooling/mold making service, we will quote you a Powder Metallurgy mold price in 24 hours!
Best Powder Metallurgy Dies Manufacturer Company In China
Pintejin Group is a machinery factory specializing in Cnc Machining, ceramic molds, industrial structural ceramics, electronic ceramics, powder metallurgy molds, filter molds, with advanced processing and testing equipment. In addition, it undertakes the business of tooling fixtures, product processing, fixture manufacturing, slow-moving wire processing, and mirror pulse processing. The factory was established in 1995, and now it has an area of 30,000 square meters and more than 500 employees. In 2007, a precision mold workshop was established, with fixed assets of more than 60 million and a registered capital of 20 million. With Japanese-made Sodick slow-moving wire Seibu ultra-precision slow-moving wire, Japan-made Sodick mirror pulse, Makino mirror pulse, American Haas machining center, Beijing Jingdiao high-speed machining center, Taiwan-made Gentiger high-speed machining center and other advanced equipment, welcome new and old Customers come to guide. We sincerely look forward to serving and cooperating sincerely for the vast number of friends in the industry.