Aluminum Nitride Ceramic
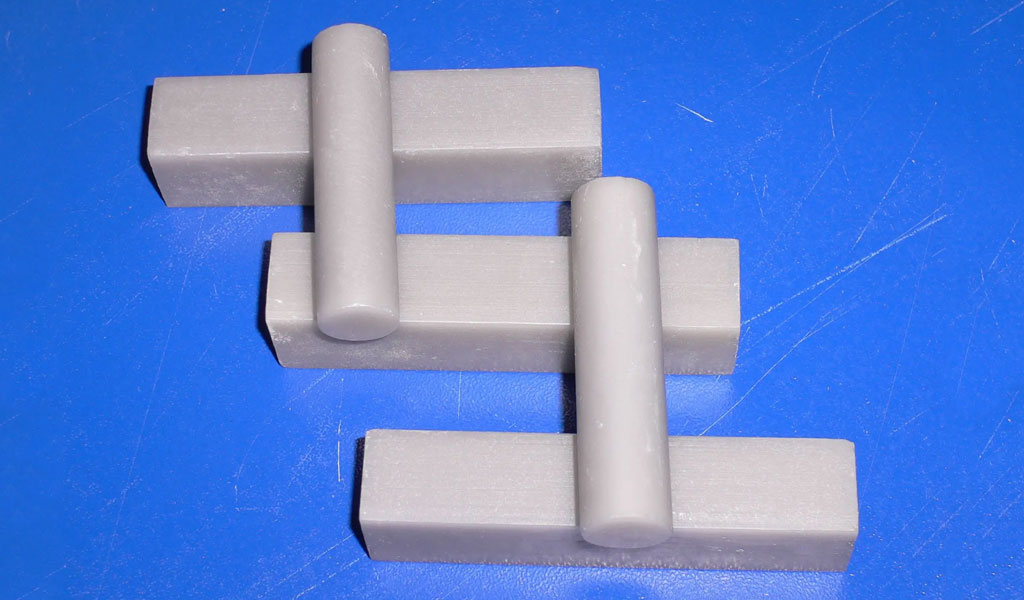
What Is Aluminum Nitride Ceramic
Aluminum nitride was a ceramic insulator (polycrystalline material was 70-210 W‧m−1‧K−1, and single crystal could be as high as 275 W‧m−1‧K−1 ), the nitrogen Aluminum has high heat transfer ability, so that aluminum nitride is widely used in microelectronics. Unlike beryllium oxide, aluminum nitride is nontoxic.Aluminum nitride, covalent bond compound, chemical formula is AIN, is an atomic crystal, belongs to diamond-like nitride, hexagonal system, wurtzite crystal structure, non-toxic, white or off-white; aluminum nitride material has ceramic type and film type.Among them, aluminum nitride ceramics are ceramics with aluminum nitride (AIN) as the main crystal phase.
Aluminum nitride (AIN) is a new type of ceramic material with excellent comprehensive properties. The aluminum nitride thermally conductive ceramic sheet has a high thermal conductivity of 180W/m . k, which is one of the materials with the highest thermal conductivity among non-metallic materials (7-10 times that of alumina ceramics). Excellent mechanical properties, good workability, high dimensional accuracy, smooth surface, no micro-cracks, bending, etc. Compared with several other ceramic machining materials, aluminum nitride ceramics have excellent comprehensive properties and are very suitable for semiconductor substrates and structural packaging materials, and have great application potential in the electronics industry.
Aluminum nitride has high thermal conductivity and good insulation performance. The resistivity is up to 4x lUfs7,”cm., the thermal expansion coefficient is small (2.55-3.8U; x i0-“K-‘, the chemical properties are stable, and it will only interact with the air at innU ℃. Oxidation. Stable to ISUU in vacuum}}. Dense aluminum nitride is water-resistant and hardly reacts with concentrated inorganic acids. Density is 3.26gIcm3, melting point is 24UU C’, elastic modulus is 3U( — 31 f7C }Pa, the flexural strength is 2sa to 350MPa, the Mohs hardness is g. AlN ceramics are prepared by powder metallurgy. Aluminum nitride films are prepared by reactive sputtering. AlU ceramic sheets are used in high-power semiconductor integrated circuits and high-power Thick die circuit, AIN film is used for the medium of thin film devices and materials with good wear resistance, heat resistance and heat dissipation
Precision CNC Machined Aluminum Nitride Ceramic Parts Manufacturer
machiningceramic.com – Pintejin is a manufacturer and fabricator of custom ceramic parts and components with aluminum nitride ceramic fast CNC machining services, we own up-to-date production equipment, advanced techniques and professional design and engineering team to support our capabilities for CNC ceramic machining and ensure the precision CNC machining ceramic parts to meet your requirements and achieve the highest quality, maintain competitive prices at the same time. CNC ceramic turning, ceramic milling, ceramic drilling, ceramic design and engineering services are available, aluminum nitride ceramic and more high specification ceramic materials at our disposal.
Advantages of CNC Aluminum Nitride Ceramic Machining
- – Aluminum Nitride Ceramic machining design and engineering assistance
- – ISO 9001:2015 quality assurance
- – Skilled operators and efficient equipment
- – Decades of experiences in CNC machining, lathing
- – Fast turnaround time and high on-time rate
- – Large production capabilities
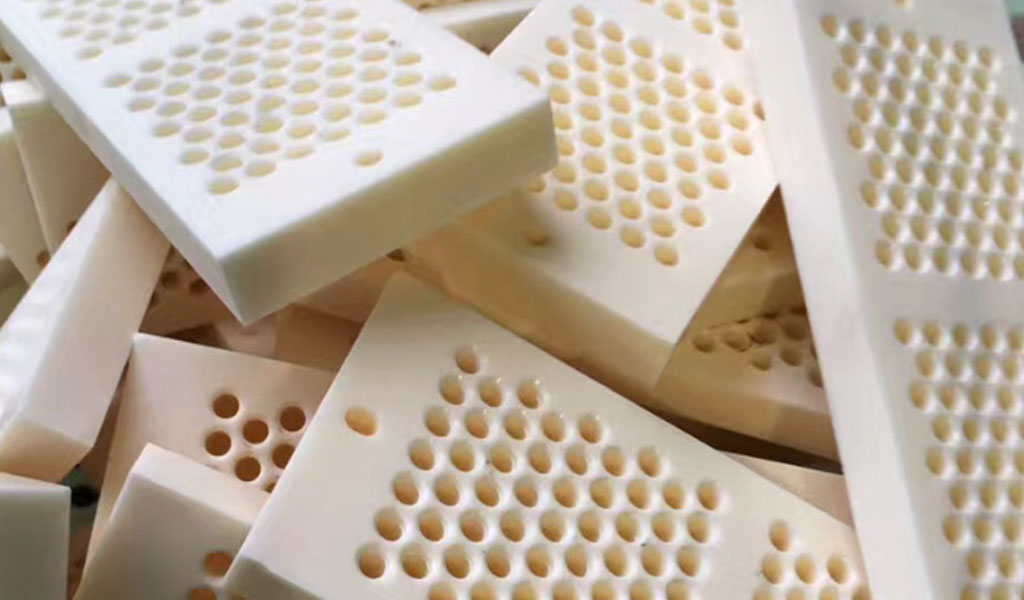
Aluminum Nitride Ceramic Machined Parts
It takes an uncommon amount of knowledge and experience to develop a thoroughly reliable supply chain for Aluminum Nitride Ceramic components. That’s why leading manufacturers turn to Pintejin for ceramic machining that delivers both needed quantities and essential quality without fail.
The Structure Of Aluminum Nitride Ceramic Material
AIN crystal is a covalent bond compound with [AIN4] tetrahedron as the structural unit, has a wurtzite structure, and belongs to the hexagonal crystal system. Chemical composition AI 65.81%, N 34.19%, specific gravity 3.261g/cm3, white or off-white, single crystal is colorless and transparent, the sublimation decomposition temperature under normal pressure is 2450℃. It is a high temperature heat resistant material. Thermal expansion coefficient (4.0-6.0) X10-6/℃. The thermal conductivity of polycrystalline AIN is 260W/(m.k), which is 5-8 times higher than that of alumina, so it has good thermal shock resistance and can withstand extreme heat of 2200℃. In addition, aluminum nitride has the property of not being attacked by molten aluminum and other molten metals and gallium arsenide, and especially has excellent corrosion resistance to molten aluminum. The performance indicators of AIN crystal are as follows:
- High thermal conductivity (about 320W/m·K), close to BeO and SiC, and more than 5 times that of Al2O3;
- The thermal expansion coefficient (4.5×10-6°C) matches Si (3.5-4×10-6°C) and GaAs (6×10-6°C);
- Excellent electrical properties (dielectric constant, dielectric loss, volume resistivity, dielectric strength);
- Good mechanical properties, the flexural strength is higher than that of Al2O3 and BeO ceramics, and it can be sintered at normal pressure;
- Good optical transmission characteristics;
- Non-toxic.
- High purity;
- It can be produced by casting process. It is a promising high-power integrated circuit substrate and packaging material.
The Application Of Aluminum Nitride Ceramic
- Aluminum nitride powder has high purity, small particle size and high activity. It is the main raw material for manufacturing high thermal conductivity aluminum nitride ceramic substrates.
- Aluminum nitride ceramic substrate, high thermal conductivity, low expansion coefficient, high strength, high temperature resistance, chemical corrosion resistance, high resistivity, low dielectric loss, is an ideal large-scale integrated circuit heat dissipation substrate and packaging material.
- Aluminum nitride has high hardness, surpassing traditional alumina, and is a new type of wear-resistant ceramic material, but due to its high cost, it can only be used for parts with severe wear.
- Using AIN ceramics with heat resistance, melt corrosion resistance and thermal shock resistance, GaAs crystal crucibles, Al evaporating dishes, magnetic fluid power generation devices and high temperature turbine corrosion-resistant parts can be made, and their optical properties can be used as infrared windows. Aluminum nitride films can be made into high frequency piezoelectric components, VLSI substrates, etc.
- Aluminum nitride is heat-resistant and resistant to erosion of molten metal, stable to acid, but easily eroded in alkaline solution. The nascent surface of AIN will react to form a very thin oxide film when exposed to humid air. Taking advantage of this characteristic, it can be used as crucible and casting mold material for smelting aluminum, copper, silver, lead and other metals. AIN ceramics have good metallization properties and can replace toxic beryllium oxide ceramics and are widely used in the electronics industry.
Development History Of Aluminum Nitride Ceramic
Aluminum nitride is a kind of ceramic material with excellent comprehensive properties, and its research can be traced back to more than one hundred years ago. It was discovered by F. Birgeler and A. Geuhter in 1862, and was discovered in 1877 by J.W. MalletS first synthesized aluminum nitride, but it had little practical application for more than 100 years, when it was only used as a nitrogen fixer as a fertilizer. Because aluminum nitride is a covalent compound, its self-diffusion coefficient is small and its melting point is high, which makes it difficult to sinter.
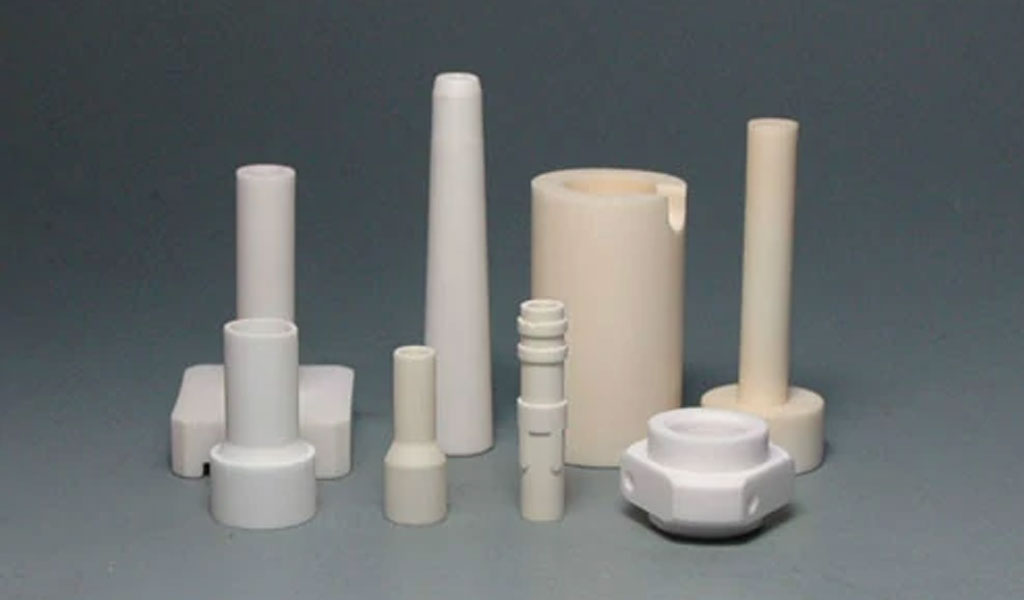
It was not until the 1950s that aluminum nitride ceramics were successfully prepared for the first time and used as refractory materials for pure iron, aluminum and Melting of aluminum alloys.
Aluminum nitride is treated with metal and can replace bauxite and beryllium oxide in a large number of electronic instruments. Aluminum nitride can be prepared by the reduction of aluminum oxide and carbon or by direct nitridation of aluminum metal. Aluminum nitride is a covalently bonded substance with a hexagonal crystal structure, the same shape as zinc sulfide and wurtzite. The space group for this structure is P63mc. Industrial grade materials can only be produced by hot pressing and welding. Substances are very stable in an inert high temperature environment.
In the air, when the temperature is higher than 700 ℃, the surface of the material will oxidize. At room temperature, oxide films 5-10 nanometers thick can still be detected on the surface of the material. Up to 1370°C, the oxide film can still protect the substance. But when the temperature is higher than 1370 ℃, a lot of oxidation will occur. Aluminum nitride is quite stable in hydrogen and carbon dioxide up to 980°C. Mineral acids slowly dissolve by attacking the boundaries of granular materials, while strong bases dissolve by attacking granular aluminum nitride. Substances are slowly hydrolyzed in water. Aluminum nitride is resistant to attack by most molten salts, including chlorides and cryolite (ie, sodium hexafluoroaluminate).
Because of its excellent thermal, electrical and mechanical properties. Aluminum nitride ceramic have attracted extensive attention from researchers at home and abroad. With the rapid development of modern science and technology, higher requirements have been placed on the properties of the materials used. Aluminum nitride ceramics will also be more widely used in many fields! Despite the unremitting efforts of many researchers over the years, great progress has been made in the research on powder preparation, forming, and sintering.
However, as of April 2013, the commercialization of aluminum nitride is not high, which is also a key factor affecting the further development of aluminum nitride ceramics. In order to promote the further development of aluminum nitride research and application, the following two research work must be done. Research low-cost powder preparation processes and methods! The main factor restricting the commercialization of aluminum nitride is the price issue.
If aluminum nitride powder can be prepared at a lower cost, its commercialization degree will be greatly improved! High-temperature self-propagating method and low-temperature carbothermic reduction synthesis process are promising powder synthesis methods. The two have the characteristics of low cost and suitable for large-scale production! Research the net near forming technology of complex shape aluminum nitride ceramic parts such as injection molding technology. It is of great significance to give full play to the performance advantages of aluminum nitride and to broaden its application range!