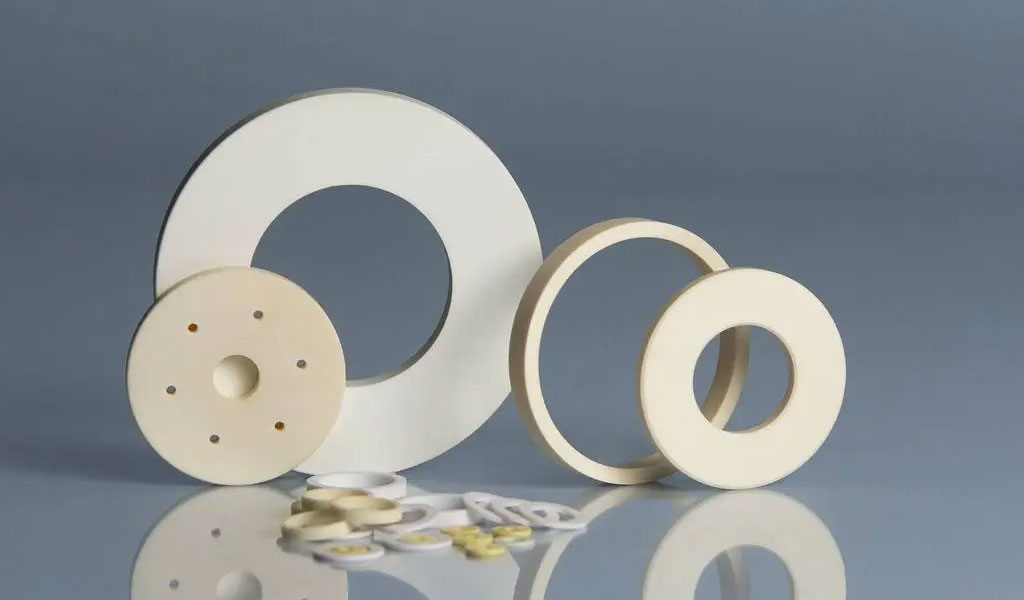
The Application Of Special Ceramics In Auto Parts
Special ceramics include zirconia ceramics and alumina ceramics. Their mechanical properties are particularly superior, so they can be processed into auto parts. Below, Pintejin Ceramics Factory will introduce the application of special ceramics in auto parts. .
1.The application of ceramics in automobile engines
The new ceramics are sintered from inorganic non-metals such as silicon carbide and silicon nitride. Compared with the alumina ceramics used in the past, the strength is more than three times that of it, and it can withstand high temperatures above 1000 degrees Celsius. The new material promotes the development of new applications in automobiles. For example, to reduce the fuel consumption of diesel engines by more than 30%, it can be said that new ceramics are indispensable materials. In the current gasoline engine, about 78% of the combustion energy is lost in the heat energy and heat transfer. The thermal efficiency of the diesel engine is 33%, which is very superior compared with the gasoline engine. However, more than 60% of the heat energy is still lost. Therefore, in order to reduce this part of the loss, the combustion chamber is surrounded by ceramic materials with good thermal insulation performance for thermal insulation, and then the exhaust gas turbocharger and power turbine are used to recover the exhaust energy. Tests have proved that this can increase the thermal efficiency to 48%. At the same time, due to the use of new ceramics, instant and quick start of the diesel engine will become possible. A turbocharger using a new type of ceramic, which has better heat resistance than today’s superalloys, but only about one-third the specific gravity of a metal turbo. Therefore, the new ceramic turbine can compensate for the low dynamic response of the metal turbine. Others that are being researched are moving parts such as piston pins and piston rings using new ceramics. Due to the weight reduction, engine efficiency is expected to increase.
2. Application of special sensitive ceramics in automotive sensors
The requirements for automotive sensors are that they can be used for a long time in the harsh environment unique to automobiles (high temperature, low temperature, vibration, acceleration, humidity, noise, exhaust gas), and should have the characteristics of small size and light weight, good reusability, and wide output range. Ceramic heat resistance, corrosion resistance, wear resistance and its potential excellent electromagnetic and optical properties have been fully utilized in recent years with the advancement of manufacturing technology, and sensors made of sensitive ceramic materials can fully meet the above requirements.
3. Application of ceramics in automobile brakes
Ceramic brakes are built on the basis of carbon fiber brakes. A carbon fiber brake disc is initially composed of carbon fiber and resin. It is pressed into shape by a machine, and then heated, carbonized, heated, and cooled to make a ceramic brake. The hardness of the carbon-silicon compound surface of the ceramic brake is close to that of a diamond. The inner carbon fiber structure makes it strong and resistant to impact and corrosion, making the disc extremely wear-resistant. At present, this kind of technology is not only used in F1 racing cars, but also involved in super civilian sports cars, such as Mercedes-Benz’s CL55 AMG.
4. The application of ceramics in automotive shock absorbers
The vibration damping device of the luxury car is an intelligent vibration damper successfully developed by comprehensively utilizing the positive piezoelectric effect, inverse piezoelectric effect and electrostrictive effect of sensitive ceramics. Due to the use of high-sensitivity ceramic components, the shock absorber has the function of identifying the road surface and self-adjusting, which can minimize the vibration of the car caused by the rough road surface.
5. Application of ceramic materials in automobile spraying technology
In recent years, ceramic thin film spraying technology, which is widely used in aerospace technology, has begun to be applied to automobiles. The advantages of this technology are good thermal insulation effect, high temperature and high pressure resistance, mature technology and stable quality. In order to achieve the goal of low heat dissipation, ceramic spraying can be applied to the engine combustion chamber components, such as zirconia sprayed on the top of the piston and zirconia sprayed on the cylinder liner. The engine after this treatment can reduce heat dissipation loss, reduce the weight of the engine itself, reduce the size of the engine, and reduce the fuel consumption.
6. Application of intelligent ceramic materials in automobiles
Smart ceramic materials classified as special ceramic products, including those used in automobile manufacturing that are sensitive to the environment and can respond sensitively to environmental changes, have become the focus of research in the field of materials science and engineering.
Pintejin machining ceramic service include : Alumina Ceramic Parts, Zirconia Ceramic, Silicon Carbide Ceramic, CNC Machined Aluminum Nitride Ceramic, Machinable Ceramic Parts, Glass Ceramic,Macor Ceramic,Powder Metallurgy Dies,Ceramic Injection Molding,Ceramic Dry Pressing,Ceramic Extrusion Dies