Silicon Carbide Ceramic
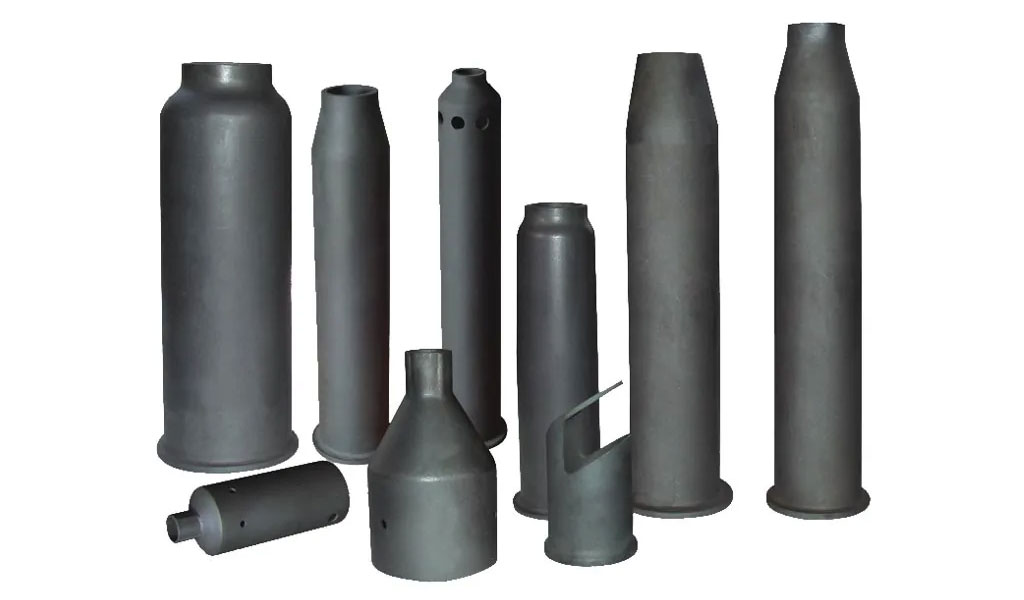
What Is Silicon Carbide Ceramic
Silicon Carbide Ceramic not only have excellent mechanical properties at room temperature, such as high flexural strength, excellent oxidation resistance, good corrosion resistance, high wear resistance and low friction coefficient, but also high temperature mechanical properties (strength, creep resistance) etc.) are the best known ceramic materials. The high temperature strength of hot pressing sintering, pressureless sintering and hot isostatic pressing sintered materials can be maintained up to 1600 ℃, which is the material with the best high temperature strength among ceramic materials. The oxidation resistance is also the best among all non-oxide ceramics(Alias Emery.).
Silicon carbide mainly has two crystal structures, namely cubic β-SiC and hexagonal – SiC. The basic structural unit of silicon carbide crystals is the interspersed SiC and CSi tetrahedra. The tetrahedrons share edges to form a plane layer, and connect with the next stack of tetrahedra at vertices to form a three-dimensional structure. Hundreds of variants have been discovered due to the formation of different structures due to differences in the packing order of the tetrahedra. Generally, the letters C (cubic), H (hexagonal), and R (rhombic) are used to indicate the lattice type, and the number of layers contained in the unit cell is used to indicate the difference.
Silicon Carbide Ceramic Machining Services – Custom Silicon Carbide Ceramic Parts China Company
Pintejin (machiningceramic.com) is a machining Silicon Carbide Ceramic China company specialized in custom silicon carbide ceramic parts manufacturing for more than 10 years, with advanced in-house equipment and tool facility, proficient machinists, and rich expertise, we can provide precision ceramic machining services and customize quality ceramic CNC machining parts with exact specification, budget prices and on-time delivery based on your requirements. In our ceramic CNC machining shop, milling, turning, drilling and more processes are available, as well as excellent surface finishing. Our lineup of ceramic and silicon carbide ceramic components can be used in broad range of industries and We are aiming to establish close and friendly cooperation with worldwide customers.
Silicon Carbide Ceramic Products And Case Studies
If you are looking for a reliable silicon carbide ceramic machining services supplier, welcome to send your inquiry to us, Pintejin can manufacture extensively custom silicon carbide ceramic parts to achieve your demands.
The Features Of Silicon Carbide Ceramic
Silicon carbide (SiC) is a compound with strong covalent bonds, and the ionic type of its Si–C bond is only about 12%. Therefore, it also has excellent mechanical properties, excellent oxidation resistance, high wear resistance and Low coefficient of friction, etc. The biggest feature of silicon carbide is its high high temperature strength. The strength of ordinary ceramic materials will be significantly reduced at 1200 ~ 1400 degrees Celsius, while the flexural strength of silicon carbide remains at a high level of 500 ~ 600MPa at 1400 degrees Celsius, so its working temperature can be Up to 1600 ~ 1700 degrees Celsius.
In addition, the thermal conductivity of silicon carbide ceramics is also high, second only to beryllium oxide ceramics in ceramics. Therefore, silicon carbide has been widely used in high-temperature bearings, bulletproof plates, nozzles, high-temperature corrosion-resistant parts, and high-temperature and high-frequency electronics. Equipment parts and other fields.
Rare earth oxides such as Y2O can also be used as sintering aids for silicon carbide ceramics, and dense silicon carbide can be obtained by liquid phase sintering. Since the liquid phase sintering reduces the porosity and improves the density through the formation of the glass phase, the characteristics of the glass phase have a great influence on the microstructure obtained by sintering.
It has excellent mechanical properties, excellent oxidation resistance, high wear resistance and low friction coefficient. The disadvantage of SiC ceramics is that the fracture toughness is low, that is, the brittleness is relatively large. For this reason, multiphase ceramics based on SiC ceramics, such as fiber (or whisker) reinforcement, heterogeneous particle dispersion strengthening, and gradient functional materials have appeared one after another. , which improves the toughness and strength of the monomer material.
The Application Of Silicon Carbide Ceramic
The initial application of SiC is that due to its superhard properties, it can be prepared into various grinding wheels, abrasive cloths, sandpapers and various abrasives, so it is widely used in the machining industry. In World War II, it was found that it can also be used as a reducing agent and heating element in steelmaking, thus promoting the rapid development of SiC. SiC ceramics have been widely used in petroleum, chemical industry, microelectronics, automobile, aerospace, aviation, papermaking, laser, mining and atomic energy and other industrial fields. Silicon carbide has been widely used in high temperature bearings, bulletproof plates, nozzles, high temperature corrosion resistant parts As well as high temperature and high frequency range of electronic equipment components and other fields.
Silicon carbide has four main application areas, namely: functional ceramics, advanced refractories, abrasives and metallurgical raw materials. The crude silicon carbide material can be supplied in large quantities, and cannot be regarded as a high-tech product, and the application of nano-scale silicon carbide powder with extremely high technological content cannot form economies of scale in a short period of time.
- As an abrasive, it can be used to make abrasives, such as grinding wheels, oil stones, grinding heads, sand tiles, etc.
- As metallurgical deoxidizer and high temperature resistant material.
- High-purity single crystals can be used to manufacture semiconductors and silicon carbide fibers.
Main application: used for wire cutting of 3-12 inch monocrystalline silicon, polycrystalline silicon, potassium arsenide, quartz crystal, etc. Solar photovoltaic industry, semiconductor industry, piezoelectric crystal industry engineering processing materials.
For Semiconductors, Lightning Rods, Circuit Components, High Temperature Applications, UV Detectors, Materials of Construction, Astronomy, Disc Brakes, Clutches, Diesel Particulate Filters, Filament Pyrometers, Ceramic Films, Cutting Tools, Heating Elements, Nuclear Fuel , jewelry, steel, protective gear, catalyst carrier and other fields.
Abrasives
It is mainly used for grinding and polishing of grinding wheel, sandpaper, abrasive belt, oil stone, grinding block, grinding head, grinding paste and monocrystalline silicon, polycrystalline silicon and piezoelectric crystal in the electronic industry in photovoltaic products.
Chemical
It can be used as a deoxidizer for steelmaking and a modifier of cast iron structure, as a raw material for the manufacture of silicon tetrachloride, and is the main raw material for the silicone resin industry. Silicon carbide deoxidizer is a new type of strong composite deoxidizer, which replaces the traditional silicon powder carbon powder for deoxidation. Compared with the original process, the physical and chemical properties are more stable, the deoxidation effect is good, the deoxidation time is shortened, energy is saved, and the Steelmaking efficiency, improving steel quality, reducing raw and auxiliary material consumption, reducing environmental pollution, improving working conditions, and improving the comprehensive economic benefits of electric furnaces are all of great value.
“Three Resistant” Material
Using silicon carbide has the characteristics of corrosion resistance, high temperature resistance, high strength, good thermal conductivity, and impact resistance. , Silicon carbide crucible, etc.
On the other hand, it can be used for high-temperature indirect heating materials in the non-ferrous metal smelting industry, such as vertical tank distillation furnace, rectification furnace tray, aluminum electrolytic cell, copper melting furnace lining, arc plate for zinc powder furnace, thermocouple protection tube, etc. ; Used to make high-grade silicon carbide ceramic materials such as wear resistance, corrosion resistance and high temperature resistance; it can also be used to make rocket nozzles, gas turbine blades, etc. In addition, silicon carbide is also one of the ideal materials for solar water heaters for highways and aviation runways.
Non-Ferrous Metals
The use of silicon carbide has high temperature resistance, high strength, good thermal conductivity and impact resistance, and is used as a high-temperature indirect heating material, such as solid pot distillation furnace, rectification furnace tray, aluminum electrolytic cell, copper melting furnace lining, zinc powder furnace arc Type plate, thermocouple protection tube, etc.
Steel
Using the characteristics of corrosion resistance, thermal shock resistance, wear resistance and good thermal conductivity of silicon carbide, it is used in the lining of large blast furnaces to improve the service life.
Metallurgical Beneficiation
Silicon carbide is second only to diamond in hardness, and has strong wear resistance. It is an ideal material for wear-resistant pipes, impellers, pump chambers, cyclones, and hopper linings. Its wear resistance is 5% of the service life of cast iron and rubber. -20 times is also one of the ideal materials for aviation flight runways.
Building Materials Ceramic Grinding Wheel Industry
Making use of its thermal conductivity, thermal radiation, high thermal strength and high thermal strength, the manufacture of thin-plate kiln furniture can not only reduce the capacity of the kiln furniture, but also improve the loading capacity and product quality of the kiln, and shorten the production cycle. Ideal indirect material.
Energy Saving
Using good thermal conductivity and thermal stability as a heat exchanger, the fuel consumption is reduced by 20%, the fuel is saved by 35%, and the productivity is increased by 20-30%, especially the internal discharge of the discharge pipeline used in the mine dressing plant, its wear resistance It is 6-7 times that of ordinary wear-resistant materials.
Abrasive particle size and its composition according to GB/T2477–83. The determination method of abrasive particle size composition is according to GB/T2481–83.
Jewelry
Synthetic Moissanite, also known as synthetic moissanite, synthetic moissanite (chemical composition SiC), has a dispersion of 0.104, which is larger than that of diamond (0.044), refractive index of 2.65-2.69 (diamond 2.42), and has the same diamond luster as diamond. , the “fire” is stronger and closer to a diamond than any imitation ever made.
Sandblasting and rust removal:
This product is made of brown corundum powder, which is extruded by high pressure and sintered at high temperature.
- Matte surface treatment of steel, steel pipe, and steel structure stainless steel products, sandblasting and rust removal before spraying.
- It is used for cleaning various molds.
- It can remove the tensile stress of various parts and increase the fatigue life.
- Cleaning and removing edge thorns before tinning of semiconductor devices and plastic packaging.
- Shot peening finishing of medical equipment, textile machinery and various hardware products.
- Cleaning of various metal pipes and non-ferrous metal precision castings and removal of burr residues
The Development History Of Silicon Carbide
Silicon carbide is a kind of carbide accidentally discovered in the laboratory by American Acheson during the fused diamond experiment in 1891. At that time, it was mistaken for a mixture of diamonds, so it was named emery, which was researched by Acheson in 1893. The method of industrial smelting silicon carbide, which is often referred to as the Acheson furnace, has been used until now. A resistance furnace with carbonaceous materials as the furnace core body is electrically heated to generate silicon carbide by heating the mixture of quartz SiO2 and carbon. Several events about silicon carbide are as follows:
- Silicon carbide was first discovered in a meteorite in 1905.
- 1907 The first silicon carbide crystal light-emitting diode was born.
- In 1955, a major breakthrough in theory and technology, LELY proposed the concept of growing high-quality carbonization, and SiC has been used as an important electronic material since then.
- In 1958, the first World Silicon Carbide Conference was held in Boston for academic exchanges.
- 1978 In the 1960s and 1970s, silicon carbide was mainly studied by the former Soviet Union. In 1978, the grain purification growth method of “LELY Improvement Technology” was adopted for the first time.
- From 1987 to now, a silicon carbide production line has been established based on the research results of CREE, and suppliers have begun to provide commercial silicon carbide bases.
The Material Variety Of Silicon Carbide
Silicon carbide has two commonly used basic varieties, black silicon carbide and green silicon carbide, both of which belong to α-SiC.
- Black silicon carbide contains about 95% SiC, and its toughness is higher than that of green silicon carbide. It is mostly used for processing materials with low tensile strength, such as glass, ceramics, stone, refractory materials, cast iron and non-ferrous metals.
- Green silicon carbide contains more than 97% SiC and has good self-sharpening properties. In addition, there is cubic silicon carbide, which is a yellow-green crystal made by a special process. The abrasive tool used to make it is suitable for super-finishing of bearings, and the surface roughness can be processed from Ra32~0.16 microns to Ra0.04~ 0.02 microns.
The Physical And Chemical Properties Of Silicon Carbide
The Material Properties Of Silicon Carbide
Because of its stable chemical properties, high thermal conductivity, small thermal expansion coefficient and good wear resistance, silicon carbide has many other uses besides abrasives, such as: coating silicon carbide powder on turbine impellers or cylinder blocks by a special process. The inner wall can improve its wear resistance and prolong the service life by 1 to 2 times; the high-grade refractory used to make it is resistant to shock, small in size, light in weight, high in strength, and good in energy saving effect. Low-grade silicon carbide (containing about 85% SiC) is an excellent deoxidizer, which can speed up steelmaking, facilitate chemical composition control, and improve steel quality. In addition, silicon carbide is also widely used to make silicon carbide rods for electric heating elements.
Silicon carbide has a very high hardness, with a Mohs hardness of 9.5, second only to the world’s hardest diamond (grade 10). It has excellent thermal conductivity and is a semiconductor that resists oxidation at high temperatures.
Silicon carbide has at least 70 crystalline forms. α-Silicon carbide is the most common allomorph, formed at high temperatures above 2000 °C, and has a hexagonal crystal structure (like wurtzite). β-Silicon carbide, a cubic crystal structure similar to diamond, is produced below 2000 °C, and the structure is shown on the page. Although in the application of heterogeneous catalyst support, it is noticeable because of its higher unit surface area than the α-type, and another kind of silicon carbide, μ-silicon carbide is the most stable, and has a more pleasant sound when colliding, But until today, these two types have not been used commercially.
Because of its specific gravity of 3.2g/cm3 and high sublimation temperature (about 2700 °C) [1], silicon carbide is very suitable as a raw material for bearings or high-temperature furnaces. It does not melt at any achievable pressure and has fairly low chemical activity. Due to its high thermal conductivity, high breakdown electric field strength and high maximum current density, many people try to use it to replace silicon in the application of semiconductor high-power components [1]. In addition, it has a strong coupling effect with microwave radiation, and all its high sublimation points make it practical for heating metals.
Pure silicon carbide is colorless, and industrially produced brown to black is due to iron-containing impurities. The iridescent luster on the crystal is due to the protective layer of silica produced on its surface.
The Material Structure Of Silicon Carbide
Pure silicon carbide is a colorless and transparent crystal. Industrial silicon carbide is pale yellow, green, blue or even black due to the type and content of impurities, and its transparency varies with its purity. The crystal structure of silicon carbide is divided into hexagonal or rhombohedral α-SiC and cubic β-SiC (called cubic silicon carbide). α-SiC constitutes many different variants due to the different stacking sequences of carbon and silicon atoms in its crystal structure, more than 70 species have been discovered. β-SiC transforms into α-SiC when the temperature is above 2100°C. The industrial method of silicon carbide is to use high-quality quartz sand and petroleum coke to refine it in a resistance furnace. The smelted silicon carbide blocks are crushed, washed with acid and alkali, magnetic separation and sieving or water separation to produce products of various particle sizes.
The Manufacturing Process Of Silicon Carbide
Due to the low natural content, silicon carbide is mostly man-made. The common method is to mix quartz sand with coke, use silica and petroleum coke in it, add salt and sawdust, put it in an electric furnace, heat it to a high temperature of about 2000 ° C, and obtain silicon carbide micropowder after various chemical processes. .
Silicon carbide (SiC) is an important abrasive because of its great hardness, but its application range exceeds that of ordinary abrasives. For example, its high temperature resistance and thermal conductivity make it one of the preferred kiln furniture materials for tunnel kilns or shuttle kilns, and its electrical conductivity makes it an important electric heating element. To prepare SiC products, the first step is to prepare SiC smelting blocks [or: SiC pellets, because they contain C and are super hard, so SiC pellets were once called: emery. But beware: it has a different composition than natural emery (garnet). In industrial production, SiC smelting blocks usually use quartz, petroleum coke, etc. as raw materials, auxiliary recycled materials and spent materials, and are prepared into a charge with a reasonable ratio and suitable particle size through grinding and other processes (in order to adjust the gas permeability of the charge, it is necessary to add an appropriate amount of The sawdust is prepared by adding appropriate amount of salt when preparing green silicon carbide) by high temperature. The thermal equipment for preparing SiC smelting blocks at high temperature is a special silicon carbide electric furnace, and its structure consists of the furnace bottom, the end wall with electrodes on the inner surface, the detachable side wall, and the furnace core body (full name: energized heating body in the center of the electric furnace, generally It is composed of graphite powder or petroleum coke installed in the center of the charge according to a certain shape and size, generally circular or rectangular. Its two ends are connected with electrodes) and so on. The firing method used by the electric furnace is commonly known as: buried powder firing. As soon as it is energized, the heating starts. The temperature of the furnace core body is about 2500°C, or even higher (2600-2700°C). When the charge reaches 1450°C, SiC begins to be synthesized (but SiC is mainly formed at ≥1800°C), and CO is released. However, SiC will decompose when ≥2600 °C, but the decomposed Si will form SiC with C in the charge. Each group of electric furnaces is equipped with a set of transformers, but only a single electric furnace is supplied with power during production, so that the voltage can be adjusted according to the characteristics of the electric load to basically maintain constant power. The high-power electric furnace needs to be heated for about 24 hours. After a period of cooling, the side walls can be removed, and then the charge is gradually removed.
The charge after high temperature calcination is from outside to inside: unreacted material (in the furnace for heat preservation), silicon oxycarbide (semi-reacted material, the main components are C and SiO), adhesive layer (it is very tightly bonded). material layer, the main components are C, SiO2, 40%-60% SiC and carbonates of Fe, Al, Ca, Mg), amorphous layer (the main component is 70%-90% SiC, and it is cubic SiC That is, β-sic, the rest are carbonates of C, SiO2 and Fe, A1, Ca, Mg), second-grade SiC layer (the main component is 90% to 95% SiC, this layer has formed hexagonal SiC, but the crystal is relatively small. Small, very fragile, can not be used as abrasive), first-grade SiC ((SiC content <96%, and is hexagonal SiC, i.e., a coarse crystal of SiC), furnace core graphite. In the above-mentioned layers, usually untreated The reaction material and a part of the silicon oxycarbide layer material are collected as spent materials, and another part of the silicon oxycarbide layer is collected together with the amorphous material, secondary products, and part of the binder as the return material, while some are tightly bonded and lumpy. The binders with high degree and many impurities are discarded, while the first-grade products are classified, coarsely crushed, finely crushed, chemically treated, dried and sieved, and magnetically separated into black or green SiC particles of various particle sizes. To make silicon carbide micropowder, it has to go through the water selection process; to make silicon carbide products, it has to go through the process of forming and sintering.