Macor Ceramic
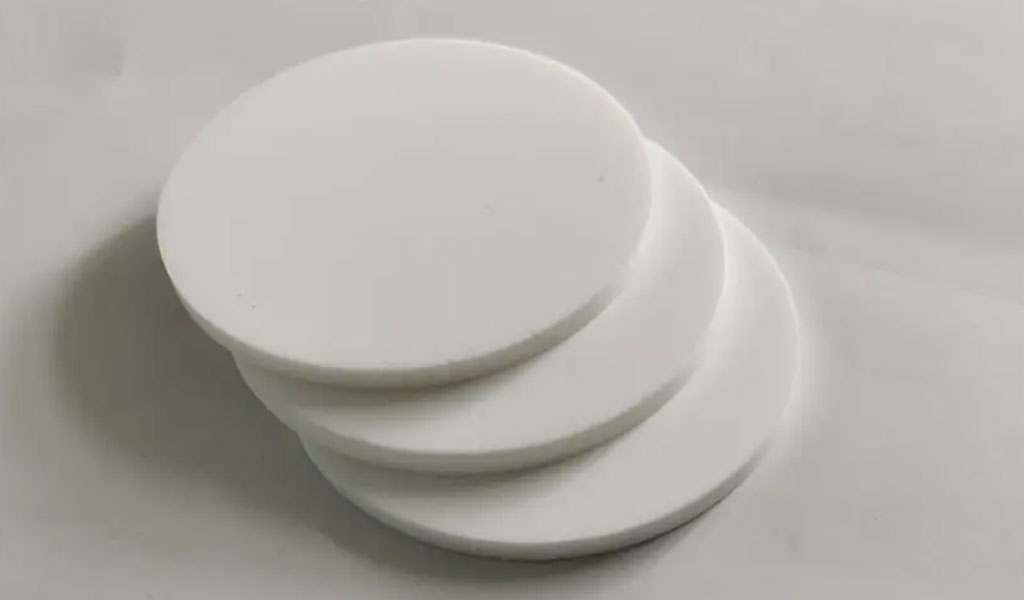
What Is Macor Ceramic
Macor ceramic is an excellent engineering material that can be machined with common metalworking tools. Macor ceramic is also a problem-solving material that combines the performance of technical ceramics with the versatility of high-performance plastics.
Macor ceramics have a high service temperature (800°C continuous to 1,000°C peak). It has low thermal conductivity and is a useful high temperature insulator as well as an excellent electrical insulator. Macor ceramic has no porosity and, when baked properly, will not outgas. It is strong and, unlike high temperature plastics, does not creep or deform. And, Macor ceramics are also radiation resistant.
Macor ceramics are pure white and can be highly polished. It can be thick or thin film metallization, brazing and epoxy bonding. Another major advantage of this unique material is that the components are economical to manufacture even in small quantities.
Macor ceramic, can be machined with common metalworking tools; allows fast turnaround without post-fire; maintains tight tolerances up to 0.0005″; withstands high temperatures up to 1000ºC (no load); clean, no outgassing and zero porosity.
With Macor ceramics, fabrication is fast because it can be quickly and inexpensively machined into complex shapes and precision parts with common metalworking tools, and no secondary firing is required after machining. This means no excruciating lead-time delays, no post-manufacturing shrinkage, and no expensive diamond tools to meet specifications.
Machining: Machining tolerances are very tight, up to 0.0005″. It can be machined to a surface finish of less than 20 inches and ground to a smoothness of 0.5µin.-AA, the configuration is limited only by the equipment available and the experience of the machinist.
Sealing, joining and metallizing: Macor ceramics can also be joined or sealed – both to themselves and to other materials – in a variety of ways: metallized parts can be welded Brazing has proven to be an effective method of joining materials to various metals; epoxy creates strong joints and seals glass to create a vacuum seal. Even simple mechanical unions are possible. It can be thick film metallized using metallic ink, or thin film metallized by sputtering.
Macor Ceramic Special Machining Technology In Pintejin
Macor ceramics can be used to make precision parts, but their processing characteristics are different from metals and plastics. Macor ceramics consist of interlocking plate-like mica crystals in a glass matrix. It is these crystals that prevent microscopic fracture and the tip from diffusing into the material, allowing it to be machined in a controlled manner. During processing, knives shatter and tear the surface of the macor ceramic, producing fine powders of crystals and glass. The crystals are very small, and when machined, macor ceramics have a good surface finish. After machining, the parts are cleaned and ready for use without further processing (eg firing).
The Configuration Of Macor Ceramic
Macor ceramics are not elastic, so when machining small or delicate parts, make sure the load is evenly distributed. If possible, use soft jaws. It is well worth spending some time understanding how the material behaves during processing. Try simple tasks like drilling, turning and milling and you’ll see how the material is machined. This information lays the foundation for good machining practice, but don’t try to use tools and speed to get the best machining performance out of your equipment.
Macor ceramics can be machined with high speed steel tools, but tungsten carbide tools are strongly recommended (tools not recommended for ceramic tips). If the macor ceramic surface is worn by the tool, or if the tool squeaks with excessive force, the tool should be stopped and sharpened.
If you are inexperienced with macor machinable ceramic, you should machine at lower speeds (keep the workpiece cool) and use a smaller depth of cut until you are confident in the machined material. It is often required to maintain a controlled machined surface finish.
The Use Coolant Of Macor Ceramic
Although macor ceramic is a high temperature resistant material, it is necessary to maintain both the material and the machining effect of the tool for best results. Water-soluble cutting fluid can improve cutting action, it can capture and wash away the debris generated during the machining process to protect the machine tool. If the fluid is to be recirculated, a settling tank is recommended. The powder produced in the process is abrasive to the machine, so attention must be paid to cleaning and machine maintenance.
The Sawing Of Macor Ceramic
Use a carbide grinding wheel blade with a speed of 30 m/min, or a diamond or silicon carbide cut-off wheel.
The Turning Of Macor Ceramic
The recommended turning speed for macor ceramic 5mm–10mm rods is approximately 600 rpm using carbide tools. The macor ceramic is lowered to 400 rpm with a 25 mm rod, a feed rate of 20-30 mm/min, a roughing depth of cut of 2-4 mm and a finishing depth of cut less than 1 mm. The side rake angle, end relief angle and side relief angle should be around 5°, the recommended side cutting edge angle is 15°–45° and the nose tip radius should be greater than 0.8mm. Thread cutting can also be performed at low spindle speeds with typical depths of cut of 0.025-0.040 mm per pass.
The Milling Of Macor Ceramic
Typical head speeds are 1000-1500 rpm with a chip load of 0.05mm per tooth. The depth of cut is the same as for turning. Climb milling prevents material from being pulled off the edge of the macro ceramic.
The Drilling Of Macor Ceramic
For machining of holes up to 5 mm in diameter in macor ceramics, the spindle speed is 1000-1500 rpm and the feed rate is 20-30 mm/min. has been proven effective. Keep loosening the drill groove, especially for small diameter holes, and check the sharpness of the drill every 25-50 holes. To prevent breakage, use a backing plate or chamfer the hole entrance and exit before drilling through the thickness. Ultrasonic drilling of macor ceramics is possible.
The Clearance Holes In Macor Ceramic
Make clearance holes one size larger than recommended for metal (typically 0.1-0.2 mm larger). Chamfer both ends of the hole to prevent chipping. A 4-flute tap is better than a 2-flute tap. Run the faucet slowly in the same direction (turning the faucet back and forth can cause debris) and rinse with water or coolant to remove dust. Wire thread inserts can be used with macor ceramics.
The Grinding And Polishing Of Macor Ceramic
Although silicon carbide and aluminum oxide wheels can be used to polish macor ceramics, diamond wheels work best. Always use water cooling. Polish with 400 grit silicon carbide prior to final polishing with alumina or ceria powder.
The Application Of Macor Machinable Glass Ceramic
Macor ceramic have the versatility of high performance polymers, the processability of metals and the properties of advanced technical ceramics. It is a hybrid glass-ceramic and offers a unique combination of properties from both material families. Macor ceramic is an excellent electrical and thermal insulator with good performance in high temperature, vacuum and corrosive environments.
One of the main advantages of macor ceramic is that it can be machined using traditional metalworking tools. This can significantly speed up turnaround and drastically reduce production costs compared to other technical ceramics, making it an excellent material for prototyping and mid-volume production.
Macor ceramics were developed decades ago on the space shuttle to prevent heat transfer to the space shuttle in the form of hinge points, retaining rings used in windows and doors, and are also used in ultra-high vacuum, CERN research Macor ceramic components are also used in the Center’s Large Hadron Particle Accelerator.
Macor ceramics are now more versatile:
- Electronic application: electronic/semiconductor/precision coil former (high precision and dimensional stability)/high voltage insulator (smooth surface and not affected by arc)
- Laser applications: gaskets, cavities and reflectors in laser assemblies (precision machining and heat resistance)
- High vacuum application: thermal fracture in high temperature processing equipment. / Coil support and vacuum feedthrough (vacuum stable and sealable)
- Aerospace/Space Industry: NASA Space Shuttle Hinges, Retaining Rings on Windows and Doors
Mounts and assemblies (thermally and electronically insulated) in multiple satellite carrier systems - Nuclear industry: fixtures and reference blocks in generator sets (dimensions are not affected by radiation)
This shows how extensive the use of macor ceramics is. It is the same that these fields have very high precision requirements for macor ceramic products, so the precision machining technology of macor ceramics is also very important.