Ceramic Dry Pressing
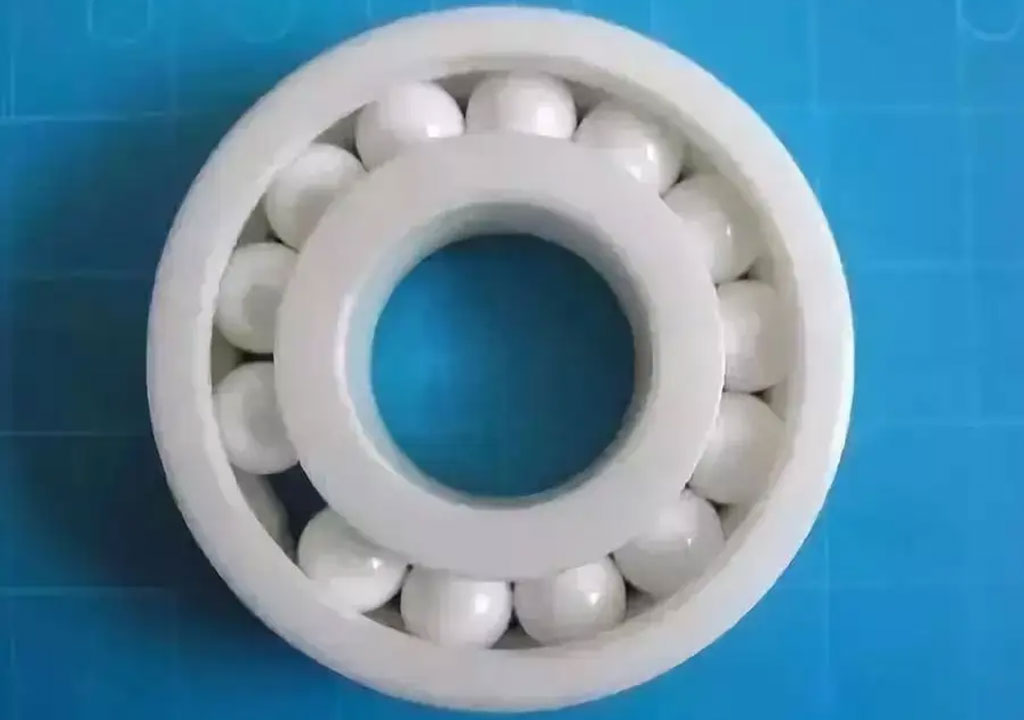
What Is Ceramic Dry Pressing
Ceramic Dry Pressing (Compression Forming) is mainly that the powder particles undergo a certain displacement and deformation after being subjected to the pressing force, and in the process of pressing and forming, as the pressure on the powder particles continues to increase, the powder particles are further extruded and finally reach densification. Press forming should ensure that the density of the pressed parts is uniform and the overall density difference is small.
Conventional methods include one-way pressurization, two-way pressurization (two-way simultaneous pressurization, two-way pressurization separately), four-way pressurization, etc. Improved dry pressing includes vibratory pressing and magnetic pressing (for metal powders).
The advantages of dry pressing are high production efficiency, less labor, low scrap rate, short production cycle, high density and high strength of produced products, and are suitable for mass industrial production;
The disadvantage is that the shape of the molded product is greatly limited, the cost of the mold is high, the strength of the green body is low, the internal compactness of the green body is inconsistent, and the uniformity of the structure is relatively poor.In the field of ceramic production, the products manufactured by dry pressing mainly include ceramic tiles, wear-resistant ceramic lining tiles, sealing rings, etc.
Ceramic Dry Pressing Fabrication Services – Ceramic Dry Pressing Parts Manufacturer
Since 2007, the team at Pintejin started to manufacture custom ceramic dry pressing parts and components for customers from a wide variety of industries. Not only CNC machining, but we also offer dry pressing mold manufacturing and other manufacturing services with our partners. We work on projects in different volumes and deliver OEM dry pressing parts in varying sizes and designs based on the capabilities of a diversity of ceramic fabrication techniques. Our experts are always on hand to provide suggestions and assistance on material selection, design improvement, and production optimization. We have been working with zirconia, alumina, silicon ni- tride, silicon carbide, aluminum nitride, microporous ceramics and more ceramic types and grades. No matter what purposes and applications of your required ceramic parts, we’ll give the best return on your payment.
The Principle Of Ceramic Dry Pressing
Ceramic dry pressing is to put ceramic powder (5% to 8% moisture content) into a metal mold, compress it under the action of force (usually unidirectional pressure), and partially discharge the gas in the void in the blank, and the ceramic.The particles are displaced, gradually approached, and tightly meshed with each other, finally forming a blank with the same cross-section as that of the mold, and the shape of the upper and lower sides determined by the upper and lower indenters of the mold.
The size of the voids in the ceramic molding body is significantly reduced, the number is greatly reduced, the density is significantly increased, and it has a certain strength.
The essence of dry pressing is that under the action of external force, the particles approach each other in the mold, and the particles are firmly connected with the help of internal friction to maintain a certain shape. This internal frictional force acts on a thin layer of binder around the particles that are close to each other. In any case, when the particles are in contact, it is equivalent to the radius of the micropores or the micropores, so that due to the pressure of the micropores, the particles will be pulled closer to each other, which is commonly referred to as “adhesion”. The dry-pressed body can be regarded as a three-phase dispersion system composed of a liquid phase (binder) layer, air, and blank. If the particle gradation and granulation of the billet is correct, and the bulk density is relatively high, the air content can be greatly reduced. As the pressure increases, the blanks will change shape, slide against each other, the gap will be filled and reduced, and the contact will be gradually increased, and they will stick to each other. As the particles are closer together, the force between the colloidal molecules and the particles is strengthened, so the green body has a certain mechanical strength. If the particle gradation of the blank is appropriate, the binder is used correctly, and the pressing method is reasonable, the dry pressing method can obtain a relatively ideal blank density.
When the ceramic powder is a very fine and barren powder, it will adversely affect the ceramic molding:
- One is the poor fluidity of the ceramic powder and the arch bridge effect, which affects the uniform filling of the mold cavity;
- Second, the finer the ceramic powder, the larger the loose height, and the larger the compression ratio, which is easy to make the density of the green body uneven;
- Third, it is difficult to discharge the gas in the pores, and it is easy to cause spallation of the green body due to the elastic after-effect. After mixing the fine powder with the binder, press it into large lumps under the pressure of 18-36MPa, then crush and sieve to make coarser pellets with good fluidity.
Due to the significantly larger size and bulk density of the agglomerates compared to the fines, the flowability is also significantly improved. The commonly used binders for granulation include PVA (polyvinyl alcohol), PEG (polyethylene glycol), CMC (sodium carboxymethyl cellulose), etc. It is necessary to consider that the binder will be burned later, so it is necessary to choose volatilization. Binders with good properties and few residual components (such as PVA) are suitable, and the dosage is generally 1% to 3% of the mass of the powder.
The Dimensions Of Dry-Pressed Products
Dry pressing, also known as pressing molding, is a commonly used method for ceramic molding. By putting ceramic powder into a metal mold and applying pressure, the pressure is about 160 tons, and the powder particles are fixed and formed by friction. Various shapes, generally suitable for forming ceramic plates, ceramic discs and other products. This molding method is simple and convenient to operate, has high production efficiency, and requires less labor. It can be realized by automated equipment. However, the disadvantage is that the ceramic density distribution formed by this method is uneven, which is not suitable for large-scale blank manufacturing and wears out the mold. larger. Dry pressing is suitable for pressing products with a height of 5 to 60 mm, a diameter of 5 to 600 mm and a simple shape.
The Pressurization Method And Pressure Distribution
In dry pressing, there are two types of pressing methods: simple pressing and double-sided pressing. Due to the different pressing methods, the friction, transmission and distribution of the pressure in the mold and between the powders are also different, so the density of the green body is also different.
1. 1-Sided Pressurization
When pressing on one side, the pressure is only pressed from the top through the die plug. At this time, due to the frictional resistance between the powders and between the powders and the die wall, a pressure gradient is generated. The lower the pressure, the lower the pressure, and the pressure distribution is uneven. , D is the diameter. The larger the L/D value, the larger the pressure difference in the green body. The pressed body has the highest density at the top and near the die wall, and the lowest density at the bottom near the die wall and the center. The pressure distribution of the single-flour compact body is less uniform.
- (a) Short mold: L/D=0.45
- (b) High mode: L/D=1.75
2. Double-Sided Pressure
Compared with single-sided pressure, double-sided pressure is pressed up and down at the same time. At this time, the situation of various frictional resistances does not change, but the effective transmission distance of the pressure gradient is shorter, and the energy loss caused by friction also decreased. In this case, the density of the green body is relatively much more uniform. The smaller the height of the product, that is, the smaller the L/D, the better the uniformity of density. Double-sided pressing, the density of the central part of the green body is small. Regardless of single-sided or double-sided pressure, if the mold is lubricated, the pressure gradient will be reduced.
The Pressurizing Speed And Holding Time
Practice has shown that the pressing speed and holding time have a great influence on the properties of the green body, that is, it has a great relationship with the transfer of pressure and the exclusion of gas. If the pressure is too fast, the pressure holding time is too short, and the gas is not easy to discharge. Similarly, when the pressure has not been transmitted to the due depth, the external force has been removed, and it is obviously difficult to obtain a relatively ideal green body quality. Of course, if the pressing speed is too slow and the holding time is too long, it is unnecessary to reduce the production efficiency. Therefore, the pressing speed and holding time should be adjusted according to the size, thickness and shape of the green body. Generally, for products with large size, thick wall, high height and complex shape, the pressure should be slow at the beginning, fast in the middle, slow in the later stage, and have a certain pressure holding time, which is conducive to the elimination of gas and the transmission of pressure. If the pressure is high enough, the holding time can be shorter. Otherwise, if the pressurization speed is inappropriate, the gas will not be discharged, and there will be bubbling, interlayer and cracks. For small sheet blanks, the requirements in this respect are not strict, and the pressing speed can be appropriately accelerated in order to improve production efficiency.
The Advantages And Disadvantages Of Dry Pressing
- Advantages: simple process, convenient operation, short cycle, high efficiency, high green body density, accurate size, small shrinkage, high mechanical strength and good electrical properties.
- Disadvantages: It is difficult to produce large green bodies. First of all, the mold wear is large, the processing is complicated, and the cost is high; secondly, the pressure can only be pressed up and down, the pressure distribution is uneven, the density is uneven, and the shrinkage is uneven, which will cause cracking and delamination. etc. phenomenon
In order to meet the high standard requirements of customers for the use environment, Pintejin will perform another isostatic pressing process on the dry-pressed product to make the ceramic body more dense!