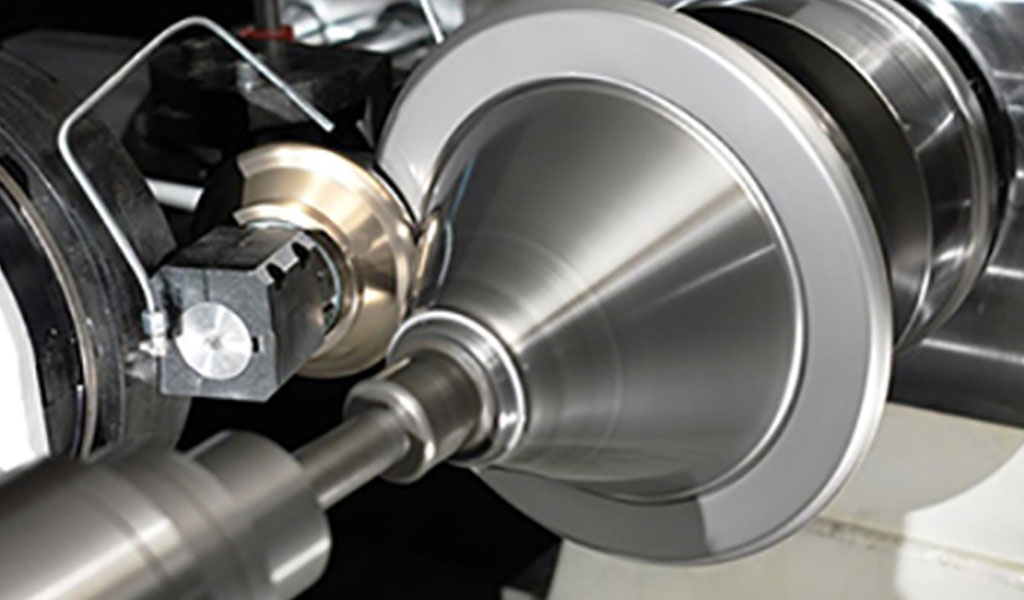
Ceramic materials have been an integral part of various industrial applications due to their unique properties, such as high hardness, thermal resistance, and chemical stability. One area where ceramics are being explored is in the manufacturing of spinning molds. Metal Spinning molds, essential in the production of spinning components for various industries, require materials that can withstand significant stresses and high temperatures. This article explores the potential and practicality of using ceramic materials for spinning molds, examining their properties, advantages, challenges, and current research in the field.
1. Background on Spinning Molds
Spinning molds are utilized in processes such as centrifugal casting and spinning casting, where materials are spun at high speeds to create uniform and precise shapes. These molds must endure extreme centrifugal forces, high temperatures, and thermal gradients. Traditional materials for spinning molds include metals like steel and alloys, which offer durability and high thermal conductivity. However, the search for alternative materials that can provide additional benefits, such as improved wear resistance and higher temperature tolerance, has led to the exploration of ceramics.
2. Properties of Ceramic Materials
Ceramic materials are known for their impressive range of properties, which include:
- High Hardness: Ceramics are typically very hard, making them resistant to abrasion and wear.
- Thermal Stability: They can withstand high temperatures without deforming, which is crucial for applications involving heat.
- Chemical Resistance: Ceramics are generally resistant to corrosion and chemical attacks.
- Low Thermal Conductivity: They have low thermal conductivity compared to metals, which can be advantageous in certain thermal management applications.
These properties make ceramics an intriguing option for spinning molds, particularly in applications requiring resistance to high temperatures and corrosive environments.
3. Types of Ceramic Materials Suitable for Spinning Molds
Several types of ceramics are considered for spinning mold applications, each with distinct characteristics:
- Alumina (Al2O3): Known for its high hardness and thermal stability, alumina is often used in high-wear and high-temperature applications.
- Silicon Carbide (SiC): This ceramic is notable for its exceptional hardness and thermal conductivity, making it suitable for high-temperature environments.
- Zirconia (ZrO2): Zirconia exhibits high toughness and thermal insulation properties, which can be beneficial in spinning molds that experience rapid temperature changes.
- Boron Nitride (BN): Boron nitride is valued for its thermal conductivity and chemical resistance, often used in applications requiring high thermal and chemical stability.
4. Advantages of Using Ceramic Materials for Spinning Molds
The potential advantages of using ceramics for spinning molds include:
- Enhanced Wear Resistance: Ceramics can withstand significant wear and tear, potentially extending the lifespan of molds.
- High Temperature Resistance: Ceramics can maintain their structural integrity at higher temperatures than many metals, which can be beneficial in high-temperature spinning processes.
- Reduced Maintenance: The durability of ceramics may lead to lower maintenance needs compared to traditional metal molds.
5. Challenges and Limitations
Despite their advantages, ceramics also present challenges in spinning mold applications:
- Brittleness: Ceramics are generally more brittle than metals, which can lead to cracking or failure under high stress or impact.
- Manufacturing Complexity: The production of ceramic molds can be more complex and costly compared to metal molds due to the need for precise fabrication and sintering processes.
- Thermal Conductivity Issues: While low thermal conductivity can be an advantage, it can also lead to uneven heating or cooling, potentially affecting the quality of the spun components.
6. Current Research and Developments
Ongoing research is addressing some of the limitations of ceramics in spinning mold applications. Key areas of focus include:
- Improving Toughness: Researchers are exploring ways to enhance the toughness of ceramics through composite materials or advanced processing techniques.
- Developing Advanced Ceramics: New ceramic materials with tailored properties are being developed to better suit the demands of spinning molds.
- Optimizing Processing Techniques: Advances in manufacturing and processing techniques are aimed at reducing costs and improving the performance of ceramic molds.
7. Case Studies and Applications
Several industries are exploring or have implemented ceramic spinning molds:
- Aerospace: The aerospace industry has shown interest in ceramic molds for their high-temperature and wear-resistant properties.
- Automotive: Automotive components that require high precision and durability are being produced using ceramic molds.
- Electronics: Ceramic molds are used in the electronics industry for the production of components that need to withstand high temperatures and corrosive environments.
8. Conclusion
Ceramic materials hold significant promise for use in spinning molds due to their unique properties, including high hardness, thermal stability, and chemical resistance. While challenges such as brittleness and manufacturing complexity exist, ongoing research and development are addressing these issues and paving the way for broader adoption of ceramics in spinning mold applications. As the technology advances, ceramics may offer a viable alternative to traditional metals, potentially improving the performance and longevity of spinning molds across various industries.
Pintejin machining ceramic service include : Alumina Ceramic Parts, Zirconia Ceramic, Silicon Carbide Ceramic, CNC Machined Aluminum Nitride Ceramic, Machinable Ceramic Parts, Glass Ceramic,Macor Ceramic,Powder Metallurgy Dies,Ceramic Injection Molding,Ceramic Dry Pressing,Ceramic Extrusion Dies